Cemented carbides are metal matrix composites made by powder metallurgy where hard carbides such as tungsten carbide (WC), titanium carbide (TiC) or tantalum carbide (TaC) are cemented into composites using tough binder metals such as cobalt and nickel. With a high hardness and excellent wear resistance, it is often difficult to grind cemented carbide into micro-sized particles, which is why ceramics with a high hardness are used as the grinding material. A water cooling system is added to quickly cool materials, thereby improving the grinding effect.
Shown below are comparison diagrams of several cemented carbides ground using our grinders. The cemented carbide particle size has been significantly reduced, and distribution is more uniform post grinding.
Grinding of tungsten carbide (WC) - Before grinding
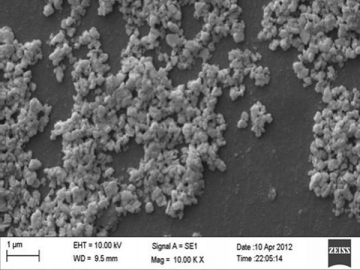
- After grinding
Characterized size | Feed | Products |
D50(μm) | 0.7 | 0.10 |
D90(μm) | 1.1 | 0.25 |
Grinding of zirconium carbide (ZrC) 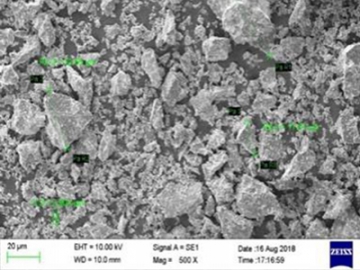
- Before grinding
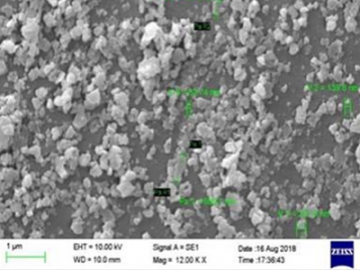
- After grinding
Grinding time | 0h | 2h | 12h |
D50(μm) | 12.4 | 0.43 | 0.18 |
D90(μm) | 37.3 | 0.68 | 0.35 |
Grinding of molybdenum carbide (MoC) 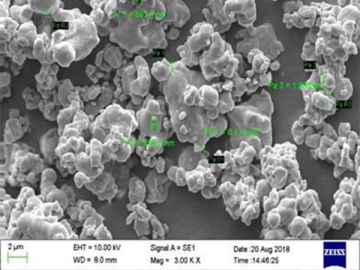
- Before grinding

- After grinding
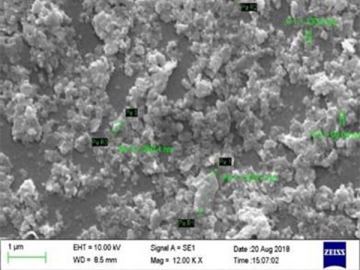
- After grinding
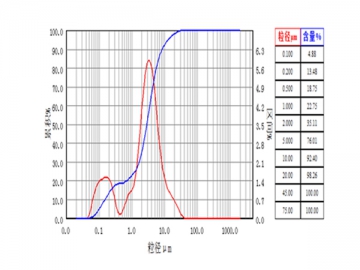
- Before grinding
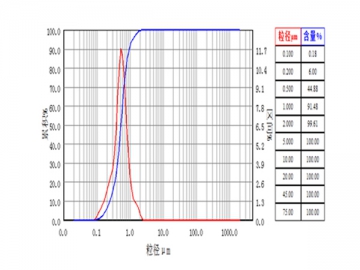
- After grinding
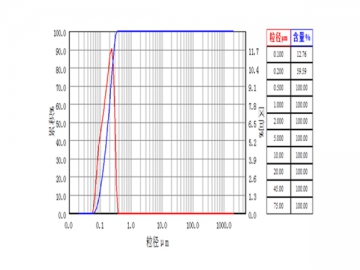
- After grinding
Grinding time | 0h | 1h | 12h |
D50(μm) | 2.86 | 0.42 | 0.12 |
D90(μm) | 8.4 | 0.94 | 0.21 |
Grinding of titanium carbide (TiC) 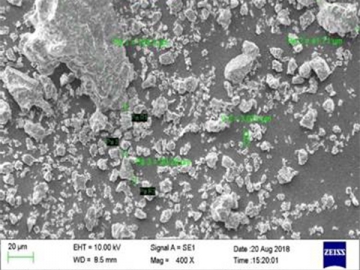
- Before grinding

- After grinding
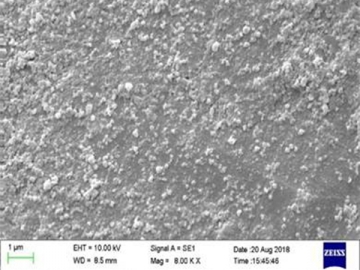
- After grinding
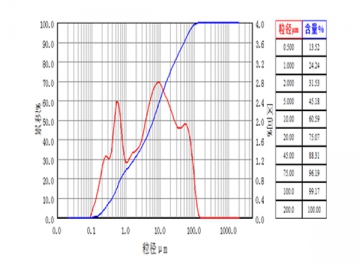
- Before grinding
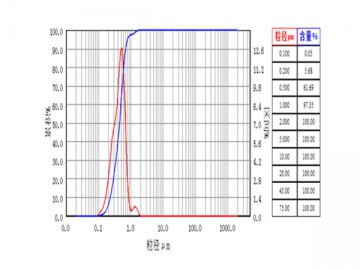
- After grinding
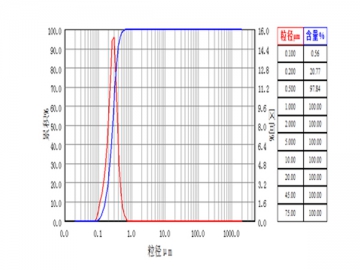
- After grinding
Grinding time | 0h | 2h | 8h |
D50(μm) | 6.3 | 0.45 | 0.15 |
D90(μm) | 50.2 | 0.69 | 0.22 |