Block Bottom Valve Bags
The block bottom valve bags are produced using AD. STAR bag making machines, thus, they are also known as AD. STAR® bags. Made from PP and PE materials, the bags can be equipped with an additional PP or PE damp resistant membrane or kraft paper liner, which gives the bag a brick shape when its filled. The top or bottom of the valve bags are equipped with valves or open mouthed after processing. The valves can be inserted into special valve bag filling machine filling spouts, allowing materials to flow through the valve and into the bag at a high speed.
To customize your valve bags, please clickApplication
These block bottom valve bags are mainly used in construction materials and food industry for filling goods materials, such as those listed below.
1. Cement
2. Building materials (like plaster, dry mortar)
3. Food
4. Pet care
5. Seeds
6. Fertilizers
7. Chemicals
8. Minerals
- Packing weight 25kg, 40kg, 50kg (or more)
- Material PP+ PE (or customers assigned)
- Fabric weight 65 g/m2
- Length 240mm to 900mm
- Width 180mm to 600mm
- Bottom 70mm to 160mm
- Printing offset printing and flexo printing, any pattern you want can be printed.
Advantages
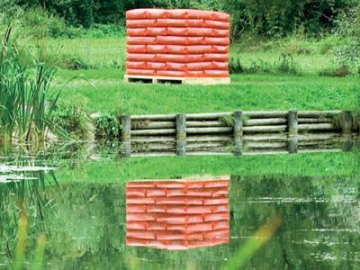
Space saving
After the filling process is complete, the brick shaped bags can be neatly stacked on top of each other. This makes it easier for pallet packaging and stacking, which saves space during storage and transportation, thus, reducing transportation costs.
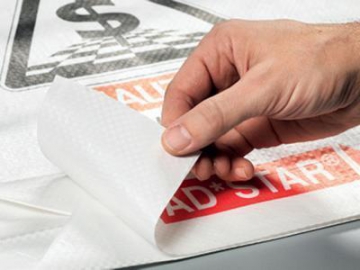
Recyclable
The bags are made from polypropylene and can be recycled after use, which beneficial for environment protection.
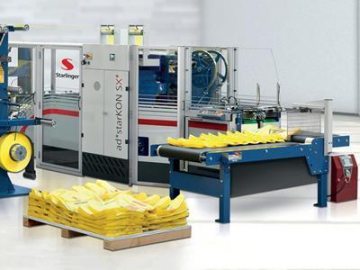
Low cost
The bags are made from coated woven fabric with a weight of half of three-layer kraft paper bags, ensuring their cost advantages and improving customer profits.
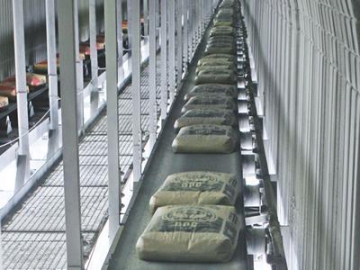
Moisture proof
Valve bags are made from coated PP woven fabric through the use of hot air welding technology, giving them a better moisture resistance over traditional kraft paper bags. The microporous technology guarantees both the bag’s moisture resistance and easy air discharge during filling, in order to facilitate the filling process.