Capability
HyCOMB follows a series of strict quality management processes throughout all production stages to avoid any application problems. We are one of the few domestic Chinese manufacturers that meet international standards in North America, Europe, the Middle East and Greater China.
Having worked with hundreds of both domestic and international projects, we are experts at meeting and providing solutions to any problems that may arise during different project conditions, as well as continuously improve our quality control.
Our laboratory features a 5-million-yuan investment for research, development and quality management of our products. The quality inspector randomly selects samples from each production process, conducts a series of mechanical and chemical performance tests in accordance with standards set by different regions using different inspection equipment, then will issue a final inspection report.
At HyCOMB, all products are produced according to the ISO 9001: 2015 quality management process standards. Our quality control is as follows: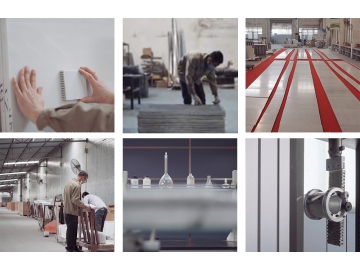
- Incoming raw material inspection for stone color differences and adhesive performance tests
- Detection and correction of production errors or discarded defective products in the production process
- Final inspection and batch inspection before leaving the factory to minimize human factors
- Continuous improvement of the inspection team through learning professional industry knowledge
- Random sample testing in the laboratory to find and fill technical loopholes
We have an automatic production line dedicated to the production of aluminum honeycomb cores, aluminum honeycomb composite panels and stone honeycomb composite panels, with an annual production of 3 million m2, 1 million m2 and 300,000 m2, respectively.
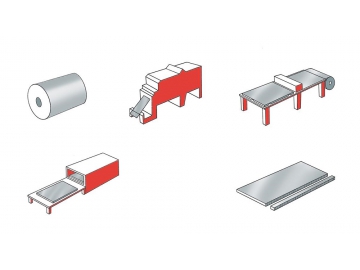
- First, an aluminum foil is precisely attached with adhesive strips of a specified width and spacing through the gluing machine, determining the aperture of the finished aluminum honeycomb core.
- Then, the aluminum foil with adhesive strip is cut by a CNC device developed by HyCOMB and stacked neatly. The precision of this manufacturing process determines whether the hexagons of the finished honeycomb core are evenly distributed.
- Next, the aluminum foil stack is hot pressed by a hot-pressing machine and the adhesive strips are thermally cured.
- After cooling, experienced technicians cut the stacked blocks into honeycomb core stacks with different thicknesses using a machine tool, pull them apart and cut them right into aluminum honeycomb core.
- Hurricane wind pressure test-NOA Miami Dade County
- Fire test-BS476, WH
- Aging resistance test-Warnock Hersey (WH) Certificate
- Freeze-thaw test-ATSM C67-11
* The NOA hurricane test report in Miami, USA (Miami Dade County, Florida. NOA No. 15-0415.07) shows that HyCOMB panels and installation systems will not come off, even under strong wind pressures of hurricanes, and will remain intact even in high-speed impact simulation experiments with hurricane debris.