Grinding Mills
For over 60 years, CITIC Heavy Industries (CITIC HIC) has focused on providing global customers with reliable, energy-saving and high-efficiency mineral grinding equipment relying on its advantages of technological development strength, core manufacturing expertise, strict quality control measures and excellent customer service.
Our technical team and sales experts can help you identify the best solution for your mineral grinding applications through a complete service system including mineralogical analysis, grinding mill selection, process optimization, equipment design & manufacturing, on-site installation & commissioning, spare parts supplying, operation training, and so forth.
We understand high-efficiency grinding mills don't happen by accident, what ultimately matters to it is based on deliberate integration of equipment design, manufacturing process optimization, material selection and quality assurance.
To date, CITIC HIC has cumulatively produced and delivered over 1,550 mineral grinding mills, with a total installed power of 3,900MW. Our large-size grinding mills hold a market share of 85% in the domestic mining market, and have been exported to more than 50 countries and regions. This means that we are a world's leading manufacturer and supplier of mineral grinding mills.
All grinding mills we provide are certified in according with ASTM, NEMA, AGMA, AWS and ANSI standards, and can be manufactured in accordance with other international standards or your local safety standards.
- Developer of national standards for grinding mills
- Holder of more than 80 patents, including over 30 invention patents
- Winner of the First Batch of Single-item Champion Demonstration Enterprise in Manufacturing Grinding Mill, prescribed by National Ministry of Industry
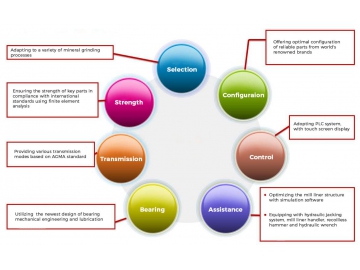
Model | Mill diameter | Mill length | Mill effective volume | Max. ball loading capacity | Rotation speed | Motor power |
mm | mm | m3 | t | r/min | kW | |
AG-40×□ | 4000 | 1400-3600 | 17-42 | 2-6 | 16.2 | 220-540 |
AG-45×□ | 4500 | 1600-4100 | 24-61 | 3-9 | 15.3 | 320-830 |
AG-50×□ | 5000 | 1800-4500 | 34-83 | 5-12 | 14.5 | 500-1200 |
AG-55×□ | 5500 | 1800-5000 | 42-112 | 6-16 | 13.8 | 630-1700 |
AG-61×□ | 6100 | 2400-5500 | 69-152 | 10-21 | 13.1 | 1050-2400 |
AG-67×□ | 6700 | 2600-6000 | 93-201 | 13-28 | 12.5 | 1500-3300 |
AG-73×□ | 7300 | 2800-6600 | 120-264 | 17-37 | 12 | 2000-4500 |
AG-80×□ | 8000 | 3200-7200 | 160-347 | 22-48 | 11.4 | 2800-6200 |
AG-86×□ | 8600 | 3400-7700 | 197-429 | 27-60 | 11 | 3500-7900 |
AG-92×□ | 9200 | 3700-8300 | 246-530 | 34-74 | 10.7 | 4500-10000 |
AG-98×□ | 9800 | 3900-8800 | 296-640 | 41-89 | 10.3 | 5600-12500 |
AG-104×□ | 10400 | 4200-9400 | 359-770 | 50-107 | 10 | 7000-15400 |
AG-110×□ | 11000 | 4400-9900 | 422-909 | 59-127 | 9.8 | 8400-19000 |
AG-116×□ | 11600 | 4600-10400 | 492-1064 | 69-148 | 9.5 | 10000-22000 |
AG-122×□ | 12200 | 4900-11000 | 580-1246 | 81-174 | 9.2 | 12000-27000 |
Model | Mill diameter | Mill length | Mill effective volume | Max. ball loading capacity | Rotation speed | Motor power |
mm | mm | m3 | t | r/min | kW | |
SAG-40×□ | 4000 | 1600-3600 | 19-42 | 13-29 | 16.2 | 310-710 |
SAG-45×□ | 4500 | 1800-4100 | 27-61 | 19-43 | 15.3 | 470-1100 |
SAG-50×□ | 5000 | 2000-4500 | 38-83 | 27-58 | 14.5 | 700-1500 |
SAG-55×□ | 5500 | 2200-5000 | 51-112 | 36-78 | 13.8 | 960-2200 |
SAG-61×□ | 6100 | 2400-5500 | 69-152 | 48-106 | 13.1 | 1400-3100 |
SAG-67×□ | 6700 | 2700-6000 | 93-201 | 65-140 | 12.5 | 2000-4300 |
SAG-73×□ | 7300 | 2900-6600 | 120-264 | 84-184 | 12 | 2600-5900 |
SAG-80×□ | 8000 | 3200-7200 | 160-347 | 112-242 | 11.4 | 3600-8100 |
SAG-86×□ | 8600 | 3400-7700 | 197-429 | 137-299 | 11 | 4600-10000 |
SAG-92×□ | 9200 | 3700-8300 | 246-530 | 172-370 | 10.7 | 5900-13000 |
SAG-98×□ | 9800 | 3900-8800 | 296-640 | 206-446 | 10.3 | 7300-16000 |
SAG-104×□ | 10400 | 4200-9400 | 359-770 | 250-537 | 10 | 9100-20000 |
SAG-110×□ | 11000 | 4400-9900 | 422-909 | 294-634 | 9.8 | 11000-25000 |
SAG-116×□ | 11600 | 4600-10400 | 492-1064 | 343-742 | 9.5 | 13000-30000 |
SAG-122×□ | 12200 | 4900-11000 | 580-1246 | 405-869 | 9.2 | 16000-36000 |
1. Mill diameter refers to the diameter inside the mill shell, while the mill length refers to the distance between two flanged ends. Effective grinding length is determined by the sizes of end liner and grate. Effective volume is the available volume inside the mill excluding the volume of shell liners and end liners, but the volume of two end cones is contained.
2. The particle size should not greater than 350mm.
3. The maximum ball loading capacity of AG mill is calculated at 3% of effective mill volume, while the SAG mill with ball loading capacity at 15% of mill volume.
4. The operating speed is usually 75% of critical speed of mill, the variable frequency speed regulation is ideally somewhere between 5% to 10% of rated speed.
Model | Mill diameter | Mill length | Mill effective volume | Max. ball loading capacity | Rotation speed | Motor power |
mm | mm | m3 | t | r/min | kW | |
MQY-09×□ | 900 | 1100-2100 | 0.6-1.2 | 1-2 | 34.8-39.5 | 11-15 |
MQY-12×□ | 1200 | 1600-2900 | 1.6-2.8 | 3-5 | 29.8-33.9 | 22-45 |
MQY-15×□ | 1500 | 2000-3600 | 3.2-5.7 | 6-11 | 26.5-30.1 | 55-110 |
MQY-21×□ | 2100 | 2700-5000 | 9-16 | 17-30 | 22.3-25.3 | 160-315 |
MQY-24×□ | 2400 | 3100-5800 | 13-24 | 24-45 | 20.8-23.6 | 250-460 |
MQY-27×□ | 2700 | 3500-6500 | 19-34 | 35-65 | 19.6-22.2 | 380-710 |
MQY-32×□ | 3200 | 4200-7700 | 32-58 | 58-108 | 17.9-20.4 | 700-1300 |
MQY-36×□ | 3600 | 4500-8600 | 45-83 | 84-154 | 16.9-19.2 | 1000-1900 |
MQY-40×□ | 4000 | 5100-8800 | 61-103 | 108-182 | 15.6-17.3 | 1400-2400 |
MQY-43×□ | 4300 | 5500-9400 | 80-132 | 141-233 | 15.0-16.7 | 1900-3100 |
MQY-45×□ | 4500 | 5800-9800 | 92-151 | 163-267 | 14.7-16.3 | 2200-3600 |
MQY-48×□ | 4800 | 6100-10400 | 111-184 | 196-325 | 14.2-15.8 | 2700-4500 |
MQY-50×□ | 5000 | 6400-11000 | 126-210 | 223-370 | 13.9-15.5 | 3100-5200 |
MQY-52×□ | 5200 | 6700-11300 | 142-232 | 250-410 | 13.6-15.2 | 3600-6000 |
MQY-55×□ | 5500 | 7100-11500 | 169-266 | 298-469 | 12.9-14.0 | 4000-6300 |
MQY-58×□ | 5800 | 7400-12000 | 196-310 | 319-504 | 12.6-13.6 | 4800-7600 |
MQY-60×□ | 6000 | 7700-12500 | 219-345 | 356-561 | 12.3-13.4 | 5400-8600 |
MQY-62×□ | 6200 | 8000-12600 | 242-372 | 371-571 | 12.1-13.2 | 5900-9200 |
MQY-64×□ | 6400 | 8200-13000 | 264-409 | 406-628 | 11.9-13.0 | 6500-10100 |
MQY-67×□ | 6700 | 8600-13500 | 304-467 | 467-716 | 11.7-12.7 | 7700-11900 |
MQY-70×□ | 7000 | 9000-13600 | 348-515 | 485-718 | 11.4-12.4 | 8600-12800 |
MQY-73×□ | 7300 | 9400-14000 | 395-577 | 570-832 | 11.2-12.1 | 10000-14700 |
MQY-76×□ | 7600 | 9800-14600 | 447-653 | 644-941 | 10.9-11.9 | 11500-17000 |
MQY-79×□ | 7900 | 10200-15000 | 501-724 | 675-977 | 10.7-11.7 | 12700-18400 |
MQY-82×□ | 8200 | 10600-15500 | 561-807 | 756-1088 | 10.5-11.4 | 14500-20800 |
MQY-85×□ | 8500 | 11000-16000 | 625-895 | 843-1207 | 10.3-11.2 | 16400-23600 |
1. Mill diameter refers to the diameter inside the mill shell, while the mill length refers to the effective grinding length.
2. The particle size should not greater than 25mm.
Model | Mill diameter | Mill length | Mill effective volume | Max. ball loading capacity | Rotation speed | Motor power |
mm | mm | m3 | t | r/min | kW | |
MQ-09×□ | 900 | 900-1800 | 0.45-0.9 | 0.96-1.9 | 34.8-39.5 | 7.5-15 |
MQ-12×□ | 1200 | 1200-2400 | 1.1-2.2 | 2.4-4.7 | 29.8-33.9 | 22-45 |
MQ-15×□ | 1500 | 1500-3000 | 2.2-4.5 | 4.7-9.7 | 26.5-30.1 | 55-90 |
MQ-21×□ | 2100 | 2200-4000 | 7-12 | 15-27 | 22.3-25.3 | 140-250 |
MQ-24×□ | 2400 | 2400-4500 | 10-18 | 21-39 | 20.8-23.6 | 210-355 |
MQ-27×□ | 2700 | 2100-5400 | 11-28 | 23-59 | 19.6-22.2 | 260-630 |
MQ-32×□ | 3200 | 3000-6400 | 22-47 | 46-98 | 17.9-20.4 | 500-1120 |
MQ-36×□ | 3600 | 3900-7000 | 36-64 | 75-135 | 16.9-19.2 | 1000-1800 |
MQ-40×□ | 4000 | 4500-7200 | 52-83 | 103-165 | 15.6-17.3 | 1400-2200 |
MQ-43×□ | 4300 | 4700-7500 | 63-100 | 125-200 | 15.0-16.7 | 1600-2500 |
MQ-45×□ | 4500 | 5000-7700 | 73-113 | 147-226 | 14.7-16.3 | 2000-3100 |
MQ-48×□ | 4800 | 5300-7900 | 89-132 | 178-265 | 14.2-15.8 | 2200-3300 |
MQ-50×□ | 5000 | 5500-8100 | 100-147 | 199-293 | 13.9-15.5 | 2600-3800 |
MQ-52×□ | 5200 | 5700-8300 | 112-163 | 224-326 | 13.6-15.2 | 3000-4300 |
MQ-55×□ | 5500 | 6000-8500 | 132-187 | 265-375 | 12.9-14.0 | 3700-5200 |
1. Mill diameter refers to the diameter inside the mill shell, while the mill length refers to the effective grinding length.
2. The particle size should not greater than 25mm.
Model | Mill diameter | Mill length | Mill effective volume | Max. ball loading capacity | Rotation speed | Motor power |
mm | mm | m3 | t | r/min | kW | |
MQG-09×□ | 900 | 900-1800 | 0.45-0.9 | 0.96-1.9 | 34.8-39.5 | 7.5-15 |
MQG-12×□ | 1200 | 1200-2400 | 1.1-2.2 | 2.4-4.7 | 29.8-33.9 | 22-45 |
MQG-15×□ | 1500 | 1500-3000 | 2.2-4.5 | 4.7-9.7 | 26.5-30.1 | 55-90 |
MQG-21×□ | 2100 | 2200-4000 | 7-12 | 15-27 | 22.3-25.3 | 140-250 |
MQG-24×□ | 2400 | 2400-4500 | 10-18 | 21-39 | 20.8-23.6 | 210-355 |
MQG-27×□ | 2700 | 2100-5400 | 11-28 | 23-59 | 19.6-22.2 | 260-630 |
MQG-32×□ | 3200 | 3000-6400 | 22-47 | 46-98 | 17.9-20.4 | 500-1120 |
MQG-36×□ | 3600 | 3900-7000 | 36-64 | 75-135 | 16.9-19.2 | 1000-1800 |
MQG-40×□ | 4000 | 4500-7200 | 52-83 | 103-165 | 15.6-17.3 | 1400-2200 |
MQG-43×□ | 4300 | 4700-7500 | 63-100 | 125-200 | 15.0-16.7 | 1600-2500 |
MQG-45×□ | 4500 | 5000-7700 | 73-113 | 147-226 | 14.7-16.3 | 2000-3100 |
1. Mill diameter refers to the diameter inside the mill shell, while the mill length refers to the effective grinding length.
2. The particle size should not greater than 25mm.
Model | Mill diameter | Mill length | Mill effective volume | Max. ball loading capacity | Rotation speed | Motor power |
mm | mm | m3 | t | r/min | kW | |
MB-09×□ | 900 | 1400-2200 | 0.7-1.1 | 1.5-2.3 | 29.7-33.5 | 11-15 |
MB-12×□ | 1200 | 1800-2500 | 1.6-2.3 | 3.6-5.0 | 25.2-28.5 | 30-37 |
MB-15×□ | 1500 | 2100-3000 | 3.1-4.5 | 7-10 | 22.3-25.2 | 75-95 |
MB-21×□ | 2100 | 3000-3600 | 9.1-10.9 | 20-24 | 18.7-21.2 | 175-210 |
MB-27×□ | 2700 | 3600-4500 | 18.2-22.8 | 40-50 | 16.5-18.5 | 360-450 |
MB-32×□ | 3200 | 4500-5400 | 32.2-38.7 | 71-85 | 14.6-16.6 | 630-800 |
MB-36×□ | 3600 | 4500-6000 | 40.8-54.4 | 90-20 | 13.8-15.6 | 1000-1250 |
MB-40×□ | 4000 | 5000-6000 | 56.7-68.0 | 125-150 | 13.0-14.8 | 1250-1500 |
MB-43×□ | 4300 | 5000-6000 | 66.0-79.2 | 145-174 | 12.5-14.2 | 1400-1800 |
MB-45×□ | 4500 | 5000-6000 | 72.6-87.1 | 160-192 | 12.2-13.9 | 1600-2000 |
MB-47×□ | 4700 | 5500-6500 | 87.4-103.3 | 192-227 | 12.0-13.6 | 1800-2200 |
1. Mill diameter refers to the diameter inside the mill shell, while the mill length refers to the effective grinding length.
2. The particle size should not greater than 25mm.
We believe the projects that we have executed speak for themselves. CITIC HIC has engineered and provided 6 AG mills of Ø12.2m×11m (28000kW gearless drive) and 6 overflow discharge ball mills of Ø7.9×13.6m (2×9000kW gear drive) for Sino Iron Project in Australia. For Zijin Mining's Duobaoshan Copper Mine project in Heilongjiang, we have manufactured and provided SAG mills of Ø11×6.4m (2×9000kW) and overflow discharge ball mills of Ø7.9×13.6m (2×9000kW) which have been well operating currently.
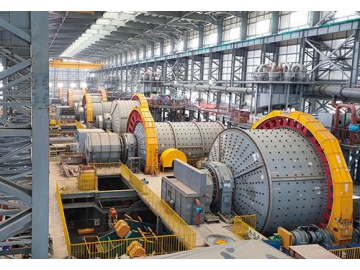
Western Mining Group's Yulong Copper Mine Project in Tibet
(Altitude 4660m 60,000t/d)
4 SAG mills, Ø8.8×4.8m
4 overflow discharge ball mills, Ø6.2×10.5m
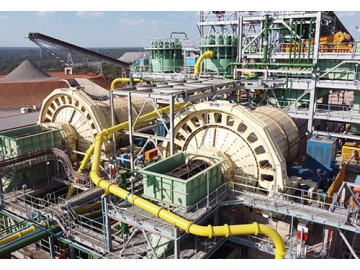
Kamoa-Kukula Copper Mine Phase I & Phase II in DR Congo
(11,400t/d)
2 overflow discharge ball mills, Ø6.1×9.75m
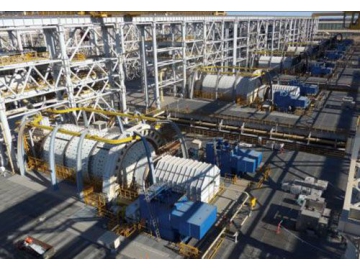
Sino Iron Project in Australia (240,000t/d)
6 overflow discharge ball mills, Ø7.9m×13.6m
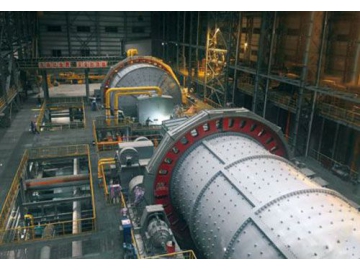
Zijin Mining's Zijinshan Gold and Copper Mine Project (45,000t/d)
1 SAG mill, Ø11×5.4m
1 overflow discharge ball mill, Ø7.9×13.6m
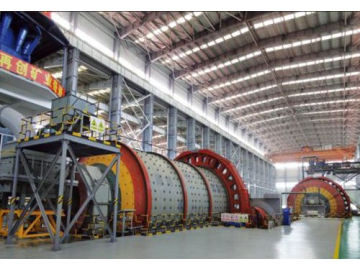
China National Gold Group's Mine Project in Inner Mongolia
Wunugetushan Copper-Molybdenum Mine Project Phase II (42,000t/d)
1 SAG mill, Ø11×5.4m
1 overflow discharge ball mill, Ø7.9×13.6m
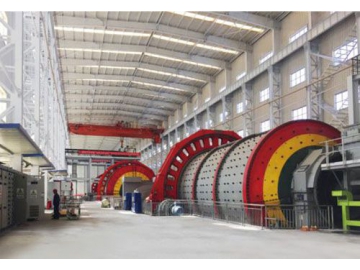
China National Gold Group's Tibet Huatailong
Jiama Copper-Polymetallic Mine Project Phase II (40,000t/d)
2 SAG mills, Ø10.37×5.19m
2 overflow discharge ball mills, Ø7.32×12.50m
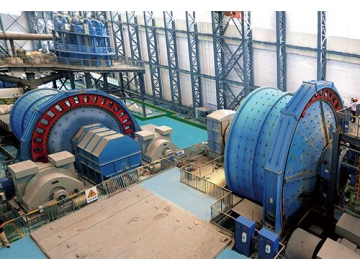
JDC Group's Molybdenum Mine Project (20,000t/d)
1 SAG mill, Ø10.37×5.19m
1 overflow discharge ball mill, Ø7.32×12m
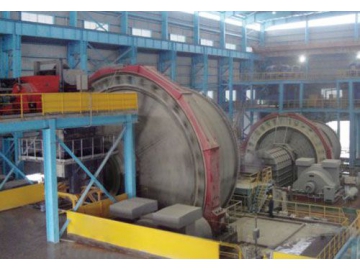
Jiangxi Copper Corporation's Dexing Copper Mine Project (22,500t/d)
1 SAG mill, Ø10.37×5.19m
1 overflow discharge ball mill, Ø7.32×10.68m
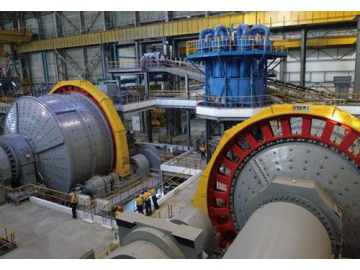
Mongolian Erdenet Mining Corporation's Copper Mine Project (20,000t/d)
1 SAG mill, Ø9.75×4.88m
1 overflow discharge ball mill, Ø6.71×9.75m
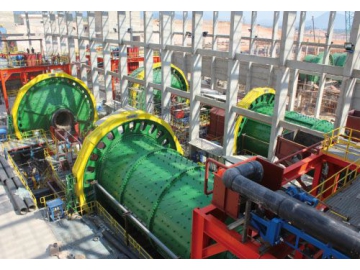
Laos Phonesack Group's KSO Gold Mine Project (83,000t/d)
6 SAG mills, Ø8.8×4.8m
1 SAG mill, Ø8.8×5.5m
6 overflow discharge ball mills, Ø6.2×11.5m
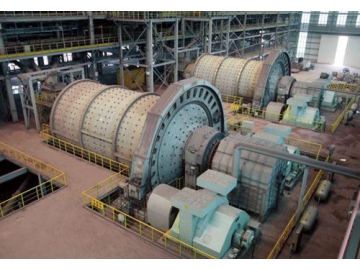
TISCO Group's Yuanjiacun Iron Mine Project (70,000t/d)
3 overflow discharge ball mills, Ø7.32×11.28m
3 overflow discharge ball mills, Ø7.32×12.50m

- High cost-effectiveness
CITIC HIC grinding mills are recognized as China's Manufacturing Industry Single Champion Product. CITIC HIC is responsible for setting the national standards of semi-autogenous mills (SAG mills) and ball mils, supported by powerful database, optimized process technology, cutting-edge design concept, and 60 years of experience in developing and nurturing innovative technology. - High operating rate
The long life cycle of our products is based on the adoption of international standards, high-quality materials, state-of-the-art processing techniques. - Low-carbon & environmental-friendly processes
Intelligent control technology coupled with long-life wear-resistant materials results in low-carbon and eco-friendly operations. - High-efficiency service
Our service network is distributed all over the world, and our service team of seasoned professionals is reliable and willing to assist along the way. We are able to deliver quick response to customer needs and provide full life cycle support via online monitoring and diagnosing, product upgrading and continuous process improvement.
- Manufacturing
Casting and Forging Capacity
We have four production lines that have the capacity to produce large steel castings, large high-value forgings, large annular parts and large non-ferrous metal parts respectively. - Service
Lifetime service
With state-of-the-art technology and rich experience, CITIC HIC works through each critical step to individualize the optimal process and performance as per customer needs. Our lifetime service covers equipment installation, testing, maintenance, refurbishing, remote monitoring & diagnosis, upgrading & retrofitting, and performance guarantee.