SD-P08 Automatic Pulp Molding Machine
Description
SD-P08 automatic pulp molding machine uses Siemens PLC system to control production process. Operators can monitor and adjust action parameters via a touch screen. A single operator can monitor multiple machines, thus saving cost. The machine can be stopped and started arbitrarily. SD-P08 automatic pulp molding machine is highly automatic, it features stable performance, easy workflow and state of the art manufacturing technology. All manufacturing process is fully automatic, from product manufacturing to collecting and counting, this machine delivers a perfect combination of manufacturing technology and mechanical properties. SD-P08 automatic pulp molding machine is sure to help our clients establish great advantage with latest technology in conquering international market.
Application
SD-P08 automatic pulp molding machine produces microwavable, freezable and distillable food packaging products including plates, bowls, trays, cups and mugs from plant fiber pulp including bagasse pulp, bamboo pulp, wheat straw pulp, reed pulp and wood pulp. Besides, it can also produce industrial packaging products.
- Plate
- Bowl
- Box
- Tray
- Cup
- Slipper
Manufacturing Process Detail
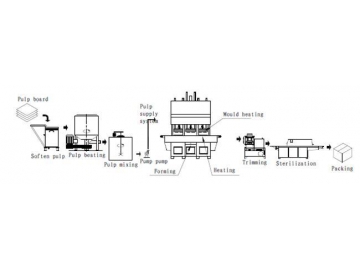
1. Pulping process takes soaked paper pulp boards and mixes them into pulp. Firstly paper boards are shredded by hydraulic pulper and taken into pulp mixing pool. After adding eatable waterproof, oil proof additives, they are taken into pulp feeding pool. They are then fed via feeding system to the automatic quantitative analyzer in the forming machine. After accurate slip casting, pulps are then stirred evenly with water and then dehydrated and formed.
2. Forming process is the most important process in the production line. Pulps are slip casted, stirred evenly with water and then dehydrated. Latest dual-vacuum-dehydrating trim-free technology in the forming mold raises qualified rate by eliminating perforation and uneven thickness. Formed product and then moved to solidifying mold for further dehydration.
3. Heating process employs patent-protected technology from our company. Compared to traditional electrical heating technology, it is 70% more energy effective and 30% more cost effective. This technology meets food packaging health standards, guarantees a 98% qualified rate as well as a high production capacity and a very good quality.
4. No further trimming process is needed after heating. Products can be directly sterilized and packaged.
SpecificationItem | Parameter | Comment |
Dimension | 4700*2500*4100mm mm | Provide by manufacturer |
Weight | 14T | Provide by manufacturer |
Workbench dimension | 850*850mm | Provide by manufacturer |
Loading capacity | 5.5KW | |
Loading time | 60s | Calculated by standard 9-cun plate (16g) |
Control range of product weight | ±1.5-2.5g | Standard weight ±1.5-2.5 |
Maximum power of heat pressing mold | 160KW | Provide by manufacturer |
Product height | ≦100 mm | |
Production Capacity Daily | 400KG (25000) | Calculated by standard 9-cun plate (16g) |
Qualified rate | ≧95% |
Feature
1. Pipes and valves which have contact with pulps are made of 304 steel, giving them very good heat-resistant, decay-resistant ability and very good mechanical properties.
2. Molds are made with 7075 aluminum, which has very good thermal conductivity, is highly wear-resistant and has high strength.
3. Energy effective hydraulic device designed by our company has been issued a Chinese patent.
4. Both electrical heating and heat transfer oil heating is available.
5. Forming method takes hydraulic power, whose pressure is up to 15Mpa. High pressure ensures high density and high strength in products.
6. Safe operating rate is up to 95%. This machine can run safely 24 hours a day.
Feature
1. SD-P08 automatic pulp molding machine is highly automatic, one single operator can monitor multiple machines thus saving cost.
2. Patent protected heat transfer oil heating technology is 70% more energy effective than traditional electrical heating. Negative pressure is used for material flow instead of using a manipulator, which greatly reduces labor.
3. Fixed steel wire gauze usage rate is 20 times higher, which reduces one fifth of production cost by reducing wearing.
4. Automatic operation flow requires 80% less operators than semi-automatic alternatives. It reduces labor intensity and prevents injury.
5. Original trim-free technology reduces cost by 10%.
6. Automatic alarm and stop function helps reduce loss.