Technological Innovation
Innovation promotes development. As a leading mold manufacturer in China, Hisense Mold has been carrying forward the innovative spirit through all stages of its development. Till today, we have held three national key research projects and two of Qiongdao City. Meanwhile, joint researches with Shandong University and Huazhong University of Science and Technology have been conducted for years. It is by such efforts that we have obtained rich fruits in the development of new technology and manufacturing processes. At the present, we have 8 invention patent letters and over 30 utility model patent letters.
1. CAE Simulation Analysis
We have introduced the Moldflow/MPI software from USA, which can effectively help us analyze each stage of the injection molding, like filling, pressure holding, cooling, gas-assisted injection and warping. Meanwhile, we have taken full use of our rich experience in the mold development while applying advanced software. It is in this way that quality and reliability of our molds is significantly promoted.
2. Hot Runner Technology
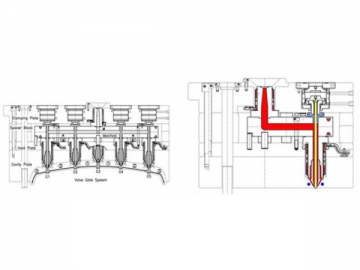
For the past years, we have obtained mature techniques on the application of hot runner and established reliable cooperative relationship with YUDO, INCOR, MOLD-MASTER, DME, SYNEVNTIVE and DELACHAUX, etc. Hereby, we can provide multiple options for the hot runner with customer. Importantly, this mature hot runner technology together with the sequential valve gate hot runner system technology can make weld lines on plastic products well controlled.
3. Gas-Assistant Injection Technology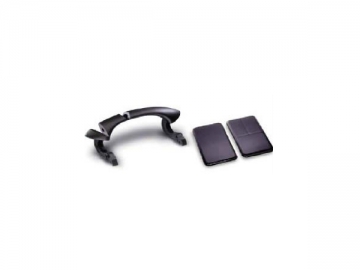
As early as 1997, we started to apply this gas-assistant injection technology in the production of precision moulds for front shells of large-screen TV sets.
- 4. IML/IMD Technology
- 5. EROWA Automated Processing Technology For Tooling Production
- 6. Large Area Micro Holes Machining Technique
1. Product Appearance Improvement
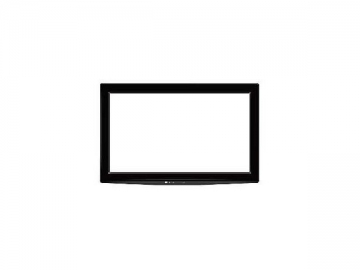
High-Gloss Mould Technique(Steam-Mould, E-Mould, EMCO-Mould)
As the latest technology of mould making, this high gloss mould technique can promote the appearance quality of products while reducing the coating spray as well as the pollution caused by it. We have adopted this technique in the production of moulds for flat-panel TV sets and monitors. According to different heating ways, there are three available models, namely the steam mould, H mould and E-mould. At the same time, we have also developed a special control box for the moulds which are also available for customers. What's more, we have obtained the use right of the E-MOULD Patent.
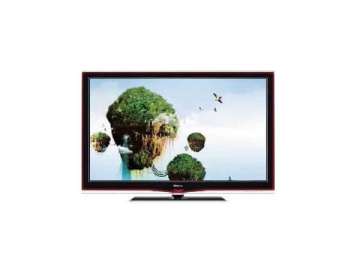
Large scale 2K-Injection Technique
This technology is mainly used to manufacture moulds for LCD/LED's front panels, sunroofs and plastic pars of autos. With this technology, surfaces of the one-step molding material and post-forming material could be blended and the plastic product(made of the two materials of two different colors) can have a large area of well blended materials. Moreover, a two-color injection molding machine together with this 2k-injection technique could make a well made product with just one complete cycle. The finished plastic product will have higher strength and surface hardness. High brightness transparent surface and gradually changed transparent edge can be made, which effectively promotes the appearance quality of the product. What's more, adoption of this technology makes the spray coating unnecessary and reduces manufacturing processes, promoting the production efficiency and rejection rate. Therefore, the labor and energy costs as well as pollution caused by spraying get significantly decreased. That is why the overall production cost of plastic products can be reduced. There is also side benefit brought forward by this technique. As the pollution to environment and harms to human health caused by the production gets reduced, manufacturers will face less green trade barriers.
Today, we have mastered 55inch large screen technology. In the future, we will exert great efforts on the development of more home appliance moulds, multimedia product moulds and automotive moulds, like moulds for air conditioners, fridges, washing machines and cars. We believe that this technology will lead to a giant leap of home appliance quality.
- 2K-Injection Technique for Keys
- Over-Mould Technology
2. Cost Reduction Solution
Short Cycle Time & High Efficiency Technique
Based on the our own research institutes and cooperative academic institutes like Shandong University, we are able to provide a shortest molding cycle by adopting the CAE analysis and optimizing mold structure, runner system and cooling system, etc. Now we can keep the cycle time of 42inch front cover within 40s.
Stack Molding Technology
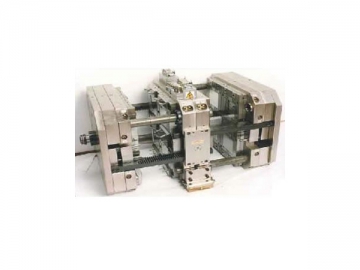
Thin-wall Molding Technology
By using the advanced CAE simulation analysis, CAD structural optimization as well as the optimization of product design(we can provide related technical supports), we can help produce thin-walled products without changing the clamping force.
Reverse & Cold-Runner-Free Mould Technique
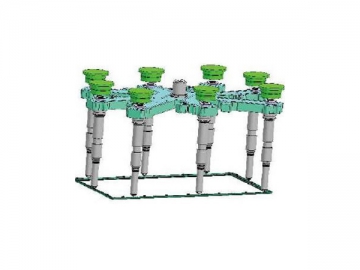
3. New Technique
- Foaming Technique
- Counter pressure Technique
- Injection compression Technique