Machine Retrofitting for Tissue Paper Industry
Whether you're operating a new or established paper mill, the ultimate goal is to maximize reliability and optimize performance.
Paper machine retrofitting is an effective approach to address production technology bottlenecks, reduce costs, enhance safety, and improve energy efficiency. We provide comprehensive technical retrofitting tissue machine solutions, with a close study and understanding of the machine or its certain components which can be enhanced or replaced to assist customers in achieving their upgrade goals.
We provide an extensive selection of paper machine components and reconstruction services that encompass everything from enhancing and replacing machinery parts to completely rebuilding individual sections or the entire tissue machine for its optimization and stable production.
- Develop assessments and technical plans based on customer requirements to optimize paper product quality, production yield, and resource consumption.
- Upgrade projects include improvements of paper machine speed, product quality, energy consumption, as well as structural modifications of the paper machine, such as converting from a cylinder paper machine to a crescent former paper machine.
- Improve production speed
- Enhance product quality
- Reduce production consumption
- Enhance equipment safety and operational performance
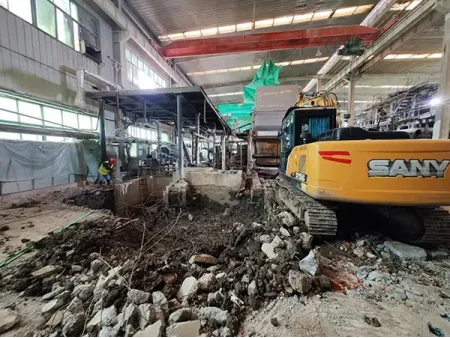
Bingzhi Machinery expertly retrofits paper machines to meet specific operational needs, enhancing performance and efficiency as demonstrated by our successful transformation of a vacuum cylinder machine into a high-speed crescent former in Sichuan Province, China.
The original paper machine was a vacuum cylinder paper machine with a speed of 600m/min. However, it had low machine speed, small production volume, and high consumption. After conducting on-site investigations and analyzing the usage and operational parameters of the existing equipment, including water, electricity, and steam, it was determined that under the principle of maximizing the utilization of the original equipment, the paper machine could be upgraded to a crescent former paper machine with a speed of 900m/min. This upgrade aimed to improve paper production quality, reduce production costs, and increase the machine speed.
The retrofitting focused on optimizing the processes of the forming section, headbox, forming rolls, guide rolls, various components in the wire section including saveall, air control, vacuum system, and hot air system. The Yankee dryer and felt section equipment and structure did not require major changes. After the transformation, the paper machine operated stably, achieving the working speed of 900m/min, and the daily production increased by more than 10 tons. Various consumption indicators and chemical usage were reduced to different extents, successfully achieving the goal of technological upgrade.
If your paper mill seeks to optimize existing equipment with proven results, contact us to explore how we can tailor solutions to elevate your paper production capabilities.