Air Compressor for Plastic Processing
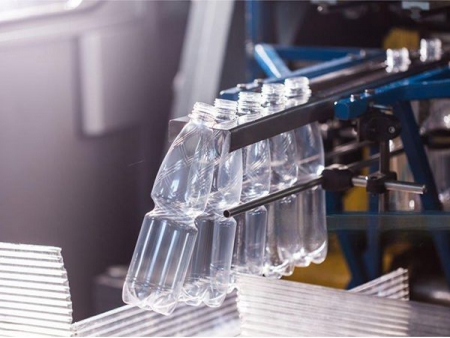
In the realm of injection molding, gas-assisted injection molding technology stands as an imperative procedure. Almost all thermoplastics (PS, HIPS, PP, ABS, and so forth) can be molded with the assistance of this gas technology. Employed in a plethora of plastic products, from television and refrigerator casings to automotive plastics and household appliances, gas-assisted injection molding takes advantage of the unique features of compressed air technology. It bolsters both the efficiency and the quality of injection-molded products.
HAREYES screw compressors are the go-to choice for injection molding applications. The components in these compressors are relatively few, yet they bring ideal dynamic balance. This allows the machinery to operate at high speeds smoothly, ensuring longevity and reliable performance.
Vacuum forming stands apart from primary molding techniques like injection and extrusion. This plastic thermoforming process aims at plastic sheets rather than granules or resins, employing heat, vacuum, and pressure to mold the sheets into intricate shapes and dimensions. The strategy doesn't rely solely on mechanical means, such as cutting.
In vacuum forming machinery, the compressed air system often consists of an air compressor, an air storage tank, main pipelines, and various valves. These machines typically operate at a pressure range of 0.4-0.5MPa. Piston air compressors and large-scale screw compressors are commonly used. The air compressors do more than just provide compressed air for molding; they offer the power for demolding, external cooling, and manipulating the mold frames.
Our experts are happy to answer all your questions and concerns as well as sales and after-sales service.