PAD Flange Mount Speed Reducer
Our PAD series planetary speed reducer are produced with a round output flange and a hollow shaft output that work together to provide excellent motor drive transmission operation.
These PAD speed reducers are commonly applied for use in printers, belt conveyers, gantry robots, auto packing and sealing machines, dispenser units, loader robots, etc.
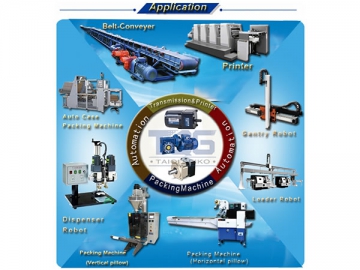
Model No. | Unit | Stage | Ratio | PAD047 | PAD064 | PAD090 | PAD110 | PAD140 | PAD200 | PAD255 |
Rated Output Torque | Nm | 1 | 4 | 19 | 50 | 133 | 278 | 555 | 1050 | 1700 |
5 | 22 | 60 | 160 | 330 | 650 | 1200 | 2000 | |||
7 | 19 | 50 | 140 | 300 | 550 | 1100 | 1800 | |||
10 | 14 | 40 | 100 | 230 | 450 | 900 | 1500 | |||
2 | 20 | 19 | 50 | 133 | 278 | 555 | 1050 | 1700 | ||
25 | 22 | 60 | 160 | 330 | 650 | 1200 | 2000 | |||
35 | 19 | 50 | 140 | 300 | 550 | 1100 | 1800 | |||
40 | 19 | 45 | 120 | 260 | 500 | 1000 | 1600 | |||
50 | 22 | 60 | 160 | 330 | 650 | 1200 | 2000 | |||
70 | 19 | 50 | 140 | 300 | 550 | 1100 | 1800 | |||
100 | 14 | 40 | 100 | 230 | 450 | 900 | 1500 | |||
Max. Output Torque | Nm | 1,2 | 4-100 | 3 Times of Normal Output Torque | ||||||
Rated Input Speed | Rpm | 1,2 | 4-100 | 5000 | 5000 | 4000 | 4000 | 3000 | 3000 | 2000 |
Max. Input Speed | Rpm | 1,2 | 4-100 | 10000 | 10000 | 8000 | 8000 | 6000 | 6000 | 4000 |
Micro Backlash P0 | Arcmin | 1 | 4-10 | ≤1 | ≤1 | ≤1 | ≤1 | ≤1 | ≤1 | ≤1 |
2 | 12-100 | ≤3 | ≤3 | ≤3 | ≤3 | ≤3 | ≤3 | ≤3 | ||
Precision Backlash P1 | Arcmin | 1 | 4-10 | ≤3 | ≤3 | ≤3 | ≤3 | ≤3 | ≤3 | ≤3 |
2 | 20-100 | ≤5 | ≤5 | ≤5 | ≤5 | ≤5 | ≤5 | ≤5 | ||
Standard Backlash P2 | Arcmin | 1 | 3-10 | ≤6 | ≤6 | ≤6 | ≤6 | ≤6 | ≤6 | ≤6 |
2 | 20-100 | ≤8 | ≤8 | ≤8 | ≤8 | ≤8 | ≤8 | ≤8 | ||
Torsional Rigidity | Nm/arcmin | 1,2 | 3-100 | 8 | 13 | 30 | 80 | 150 | 450 | 1010 |
Max. Radial Force | N | 1,2 | 3-100 | 43 | 125 | 235 | 430 | 1300 | 3064 | 5900 |
Max. Axial Force | N | 1,2 | 3-100 | 990 | 1050 | 2850 | 2990 | 10590 | 16660 | 29430 |
Service Life | Hr | 1,2 | 3-100 | 22000hrs | ||||||
Efficiency | % | 1 | 3-10 | ≥97% | ||||||
2 | 20-100 | ≥94% | ||||||||
Weight | Kg | 1 | 4-10 | 0.7 | 1.3 | 3.2 | 5.8 | 12.3 | 33 | 57.9 |
2 | 20-100 | 1 | 1.5 | 4.1 | 7.6 | 16.8 | 38 | 72.6 | ||
Operating Temperature | ℃ | 1,2 | 3-100 | (-15℃~+90℃) | ||||||
Lubrication | 1,2 | 3-100 | Synthetic Grease | |||||||
Protection Class | 1,2 | 3-100 | IP65 | |||||||
Mounting Position | 1,2 | 3-100 | Any Direction | |||||||
Noise Level | dB(A) | 1,2 | 3-100 | ≤56 | ≤58 | ≤60 | ≤63 | ≤65 | ≤67 | ≤70 |
1. High precision
Accurate positioning is realized with backlash less than 3 arc-min.
2. High rigidity and torque
Rigidity and torque are maximized with the gearbox’s single piece roller bearing.
3. High load capacity
The gear box’s outstanding load capacity is possible using its tapered roller bearing as the main bearing.
4. Methods of flange and connector
The flange and connector of the gearbox can match with any motor.
5. No leakage of grease
The gearbox is designed for use with high viscosity grease and features non-separated gears to avoid leakage.
6. Convenient maintenance
Grease does not need changing within the service time for easy installation.
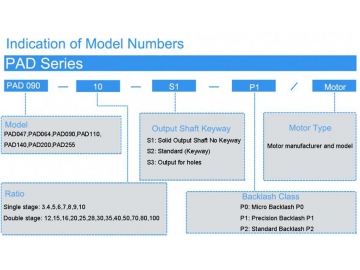
We own two multi-national patents for components used in the structure of the inner helical gear to ensure the highest output efficiency.
Patent 1: Reduce the axial thrust caused by the running of planet gears.
1. ANSYS technology was used to carry out finite element analysis to determine the gear strength. The gear shape and lead of the gear surface are treated in order to minimize noise and impact during gear engagement. This increases the service lifetime of the gears and improves operating efficiency.
2. The gears of the gearbox are made of superior quality alloy steel that has been treated with carbon-nitrogen copermeation to provide maximum wear and impact resistance.
3. The output planet carrier of the gearbox features an integrative design with its double bracing structure. The front and back bearings are distributed along a large span within the box, forming a stable one-piece structure for high torque and precision.
4. The gear ring and output housing are integrated and constructed using high quality hot forged steel, giving the gearbox added strength and durability with additional density. The integrated design ensures the geometric dimensions are accurate and provide maximum precision and strength during operation compared to other structures like built-in and clamp-on units.
5. The design of the input shaft and lock up unit features a uniform distribution to achieve dynamic balance. The double bolts are locked in place to prevent transmission slipping with the motor shaft. Zero backlash is realized.
Prior to choosing a gearbox, specify the gear ratio that you need. After this is selected, multiply the rated torque of the servo motor by the ratio. The value should be less than our gearbox rated output torque, which can be found in the attached data sheets. You should then take the other overloads which drive the motor into consideration to choose the maximum operating torque. This should not exceed 2 times that of our gearbox rated torque.
Once that is decided, you can choose the gearbox with the smallest volume to achieve maximum savings. You can send servo motor dimension drawings for model selection or advise the specific servo motor model number.
If you have any special requirements, please let us know.
Step 1: Wipe off the anti-rust agent and grease on the motor shaft
Step 3: Turn the input shaft until the cap screw is seen. Make sure the cap screw is loosened.
Step 6: Re-install the rubber plug. Finish the installation.
1) Keep the reducer in a clean and dry place.
3. Caution for operation:
2) The reducer was already filled with lubrication oil. You can use it right now.
4. Caution during operation:
2) Input speed cannot exceed the proper max. speed.
Sudden temperature rise
Unstable speed
The following cost and damages are not included in our warranty:
2) If the Reducer connects with or inserts in a unit, when we dismounting or mounting on the unit and other extra action, there will be a cost. (this is not covered in the warranty)
4) Other derivative and accompanying damages.