Three-piece Can Production Line
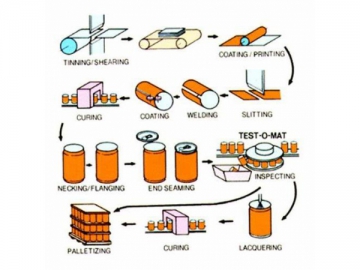
The most commonly used cans are three-piece sanitary cans which consist of a body and two end pieces that are joined together to provide a hermetic, or perfect, seal. Most commonly used for foods that are heat processed they are also used for packaging powders, syrups, and many other products that are not heat-processed. The most common shape is a round cylinder but square and oval flat cans are used, particularly for seafood processing.
Major metallic packages made of tinplate include can bodies, basic shells (BS), easy-open ends (EOE), metal crown lids, twist-off lug caps, metal rings, and EOE ring tabs. Common empty cans include three-piece cans for beverages, DI steel cans, DRD cans, spray cans, 18-liter cans, and irregular cans, of which three-piece cans are the most important empty can type. The production process of three-piece cans includes slitting, body rounding, welding, striping and capping. Although the process is complicated, a can-body combined machine can complete all the production steps with ease.
An automatic empty-can production line is made up of a can-body combined machine, a two-way slitter, a welder, weld joint protection stripping/curing system, an internal spraying/curing system (optional), an inline detecting machine, an empty-can stacking machine, strapping machine, and wrapping/shrink packaging machine. Currently, a can-body combined machine can complete can-making steps such as slitting, necking, swelling, flanging, beading, first seaming, and second seaming at a maximum speed of 500 CPM.
Three-Piece Can Manufacturing Process:Feeding → slitting (slitter) → can body rounding (automatic canbody welder) → weld joint striping (spraying and drying equipment) →capping (seamer)