Oil and Gas Fired Steam Boiler
Rated steam output: 0.5-20t/h
Rated working pressure: 0.8-2.0Mpa
Fuel type: natural gas, heavy oil, light oil, city gas and methane.
The steam boiler is high pressure boiler and changes steam into water in order to heat water through the use of a heat exchanger. It provides heat for steam powered manufacturing equipment or general heating.
The steam boiler is used in a variety of industries, with the main applications listed below.
- Food industry: The steam can be used for cleaning, as well as heating, drying or disinfecting food.
- Spinning, printing and dying industry: used for dying, rinsing and shaping of cloth.
- Biological medicine industry: used for heating reaction kettles, condensation reaction, exchanging heat and disinfecting of chemical reaction systems.
- Hospital: used for disinfecting, heating, and air conditioning.
- Petrochemical Industry: used for heating oil in order to increase liquidity.
- Wood furniture industry: used for drying wood, brick and other materials.
- Papermaking industry: High pressure steam is used to drive power generation. After decompressing, the steam is used for drying, and the last of the low-pressure steam is used for ink removal, pulping or paper production.
- Tobacco industry: can provide heat for making pipe tobacco and baking.
Type | ||||||||||
Rated steam output( t/h ) | 1 | 2 | 4 | 6 | 8 | 10 | 15 | 20 | ||
Rated working pressure( Mpa ) | 0.7/1.0/1.25/1.6 | |||||||||
Rated steam temperature(℃) | 170/184/194/204 | |||||||||
Water supply temperature(℃) | 20 | 20 | 20 | 104 | 104 | 104 | 104 | 104 | ||
Water volume( m3) | 2.7 | 4.8 | 7.4 | 11.2 | 14.1 | 16.8 | 25.2 | 34.6 | ||
Design heat exchange area( m3) | 34.2 | 68.2 | 142.8 | 187.7 | 266.1 | 304.2 | 464.9 | 635.5 | ||
Design thermal efficiency(%) | 100.2 | 100.4 | 100.5 | 100.6 | 100.6 | 100.6 | 100.8 | 100.8 | ||
Fuel consumption | light oil( kg/h ) | 64.8 | 127.8 | 254.9 | 330.7 | 440.5 | 550.6 | 823 | 1096.5 | |
natural gas( Nm3/h ) | 75.8 | 149.4 | 298 | 386.6 | 515 | 643.7 | 962.1 | 1281.9 | ||
liquefied gas | 25.9 | 51 | 101.7 | 132 | 175.8 | 219.7 | 328.4 | 437.6 | ||
( Nm3/h ) | ||||||||||
city gas | 169.5 | 334.2 | 666.7 | 864.9 | 1152.1 | 1440 | 2152.5 | 2867.8 | ||
( Nm3/h ) | ||||||||||
Total electric power | Oil( kW ) | 6 | 11.7 | 18.7 | 25.5 | 32.5 | 40 | 52.5 | 71 | |
Gas( kW ) | 4.5 | 9.5 | 16.5 | 22.5 | 29.5 | 37 | 48.5 | 67 | ||
Fan | Power( kW ) | 1.5 | 5.5 | 11 | 15 | 18.5 | 22 | 30 | 45 | |
Water pump | Power( kW ) | 3 | 4 | 5.5 | 7.5 | 11 | 15 | 18.5 | 22 | |
Maximum dimension of shipping part | length A ( mm ) | 3.6 | 4.3 | 5.3 | 6.1 | 6.6 | 7.3 | 7.5 | 8.1 | |
width B ( mm ) | 2.2 | 2.3 | 2.4 | 2.5 | 3 | 3 | 3.2 | 3.5 | ||
height H ( mm ) | 2.8 | 3.1 | 3.3 | 3.6 | 3.2 | 3.2 | 3.5 | 3.6 | ||
Boiler weight( t ) | 4.6 | 8.5 | 13.3 | 17.2 | 22.8 | 25.2 | 34.5 | 45.3 | ||
Main steam pipe diameter DN ( mm ) | 50 | 65 | 100 | 125 | 150 | 150 | 200 | 200 | ||
DN Assistant steam pipe diameter( mm ) | 25 | 25 | 40 | 40 | 40 | 40 | 40 | 40 | ||
Water supply pipe diameter DN ( mm ) | 25 | 40 | 40 | 40 | 50 | 50 | 65 | 80 | ||
Boiler sewage pipe diameter DN ( mm ) | 50 | 50 | 50 | 50 | 50 | 50 × 2 | 50 × 2 | 50 × 2 | ||
Continuous sewage pipe diameter DN( mm ) | 25 | 25 | 25 | 25 | 25 | 25 | 25 | 25 | ||
Safety valve diameter DN ( mm ) | 40 × 2 | 40 × 2 | 50 × 2 | 80 × 2 | 80 × 2 | 80 × 2 | 100 × 2 | 100 × 2 | ||
Chimney diameter( mm ) | 300 | 350 | 450 | 600 | 700 | 750 | 900 | 1000 |

The boiler shell is made using submerged arc welding, with all longitudinal and circumferential welding undergoing 100% radiographic testing to ensure the welding effect. An automatic argon welding process is used in the pipe and plate.
Aluminum silicate fiber and refractory mortar.
The boiler temperature is controlled under 50℃.
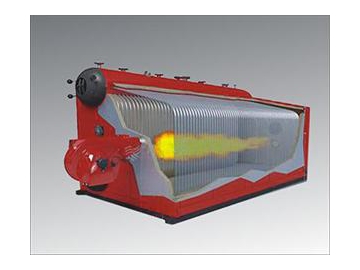
1. The industrial boiler is a natural circulation boiler with a "D" shape furnace, and a burner set in the front wall. The water wall of the furnace features a membrane structure, with the exterior of the boiler covered in a silicate insulation material and cold-rolled plate. Condensate on the tube bundle, and a convection tube bundle are both set at the outlet. Smoke goes into the convection tube bundle through the outlet of the furnace with membrane wall, through the connecting flue and into the spiral finned tube economizer, then through the chimney and into the air.
2. Micro negative pressured combustion is the main combustion process, and allows the boiler to work safely. The water wall and convective flue use a membrane wall structure for an excellent sealing and heat transfer.
3. The applicable fuel range is wide, the boiler capacity is large (10-100ton/hr), and the pressure range is large (1.0-9.8MPa).
4. The boiler heating surface is large, and the steam-water space is designed large enough to ensure the stability of the boiler parameters. The furnace has a hole for checking, which is great for usage and maintenance. The blast door is equipped at the top of the furnace, and the fully automatic burner, and continuous electric regulating unit for the water supply is used for a high combustion efficiency. The boiler also has multiple chain protection functions in order to work safely and in a reliable manner.
5. The condensing recovery device of flue gas is set at the end of the boiler, which can effectively control the temperature of exhaust smoke, and ensure a high thermal efficiency. High thermal resistance material is used as an adiabatic layer, so its thermal insulation performance is good. The outer layer of the boiler is made of a pressing shield, so the appearance is sleek and efficient.