Sandwich Panel Production Line
Sandwich panel production line of BRF series is designed and built for the production of sandwich panels with corrugated steel sheets as two skin layers. Sandwich panel production begins by uncoiling a roll of color-coated steel on an uncoiler. Roll forming is next. Later, after the steel sheets are roll formed to desired shapes, they are cut to length. Finally, these roll formed steel sheets, together with insulating cores, pass through a laminating system, where bead forming, glue application, heating, laminating, edge curling, notching, edge trimming, and cut-off operations are carried out. The entire process is computer controlled.
As an integral part of any roofing and wall panel manufacturing plants, the sandwich panel production line incorporates advanced pneumatic, electrical and mechanical mechanisms into one unit. It is best suited for producing sandwich panels with color coated steel sheets as face layers.
Features of Sandwich Panel Production Line
1. Model BRF sandwich panel processing line utilizes a computer-based stepless speed controller for steady running and easy operation.
2. A computerized position control allows users to freely adjust cut lengths. Other desirable features include the touch-screen display, automatic cuts counter (counting how many cuts have been made), and automatic error correction.
3. Customized roll forming machine can produce 10 different cross-section profiles.
4. Sheet metal profiles can be designed and corrected according to customer specific needs.
- Tongue and Groove Joint
- Butt Joint with H Section Extrusion
- Flat Roof Panel Assembly
- Corrugated Roofing Panel Assembly
Pictured below is a schematic giving you an idea of how equipment is arranged on a sandwich panel production line.
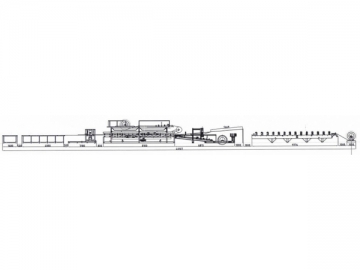
Inline Components
Uncoiler-- Double Layer roll forming machine- Feed unit ---Laminating unit—Cutting unit—Runout Table
A detailed breakdown of the insulated sandwich panel line is listed as follows.
Uncoil
Working load should not exceed 5 tons. Appropriate coil widths (color coated steel) are 1000mm and 1200mm. Coil thickness ranges from 0.3mm to 0.6mm.
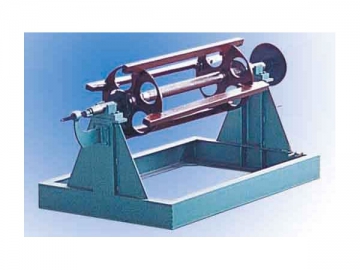
Roll Forming Machine
The roll forming process is mainly used to produce corrugated roof panels. For EPS foam boards or rockwool panels, a single-level roll former is up to the task. If you need a unit that can produce both panel types, the dual-level model might be your best bet.
We can customize a triple-level roll forming machine for the production of three different cross-section profiles. However, operators can only get one level started at a time, meaning that the three profile types can not be produced simultaneously. Rotary roller dies on the machine are precision ground on a NC lathe. Hard chrome plated and polished for durability and wear resistance.
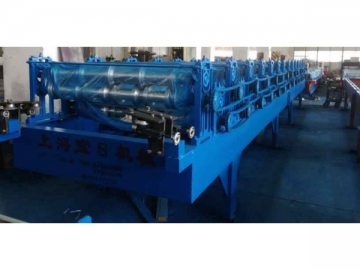
Feed Unit
The feed unit is where EPS boards and rockwool strips enter the system. Chain conveyor is used for transportation of rockwool strips due to their light weight. This conveying method saves labor and time.
Laminating Unit
Electrically controlled laminating system is where color coated steel (serving as the face layer) and EPS foams or rock strips (acting as the insulating core) are pressed tighter to form complete insulated sandwich panels. Adjustable thickness of finished insulated panels. Rigid edge curls give finished panels a smooth, cleanly look.

Cutting system
Circular saws are used to cut foam boards, enabling flat cuts. When dealing with rockwool panels, the cutting process takes place in an enclosed cabinet to prevent dust pollution and to ensure the health and safety of workers. The cutting system is computer controlled for easy operation.
Slitting machine and ridge cap rollforming machine
A simple-structured slitter, ridge-cap rollforming machine and side sealing machine are used for shaping rockwool panels.
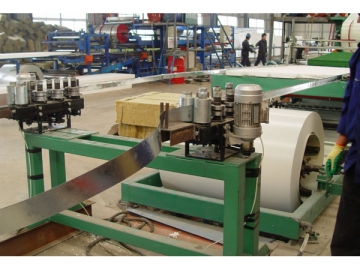
Profile and Sample of Finished Products
EPS Wall Panel (1200 and 1000)
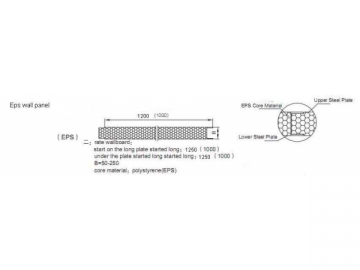
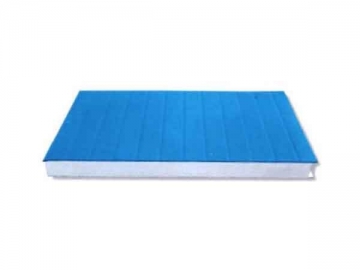
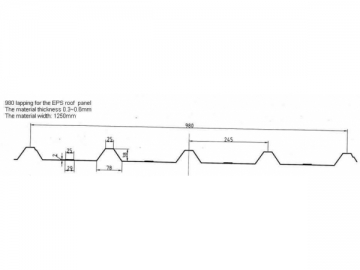
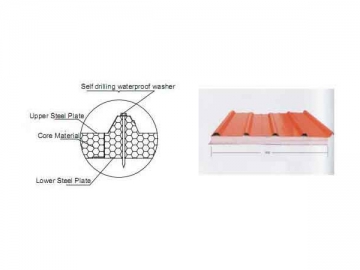
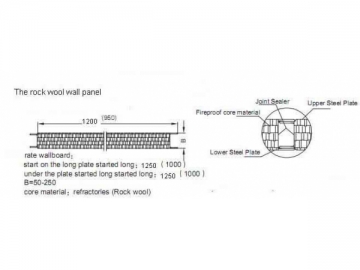
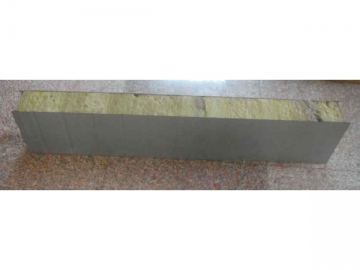
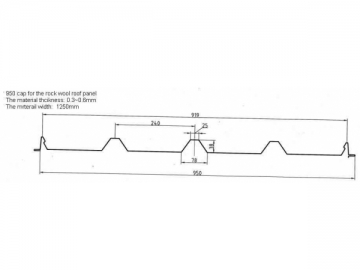
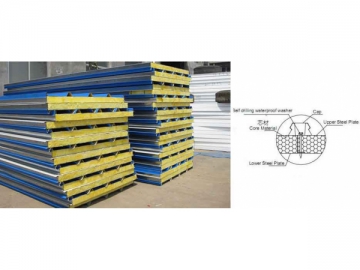
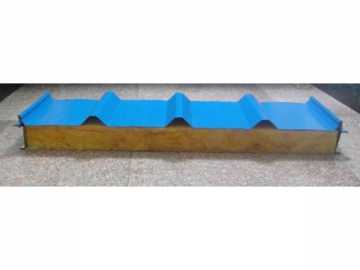
Factory Requirements
1. Workshop Dimensions: 55m x 10m x 5m
2. A 0.4~0.6m3 x 7kg compressor and smooth cement floor are needed in the workshop.
3. Shop crane with more than 5T load capacity and over 30m travel distance.
Roll Forming Materials
1. The color steel : Top Layer: 1250mm Bottom Layer: 1000mm
Thickness: 0.3~0.6mm
Coil weight less than 5T
2. Insulating Core Material: EPS foam and rock wool
EPS foam width: 975mm for roof panel
EPS thickness: 50~250mm
Rock wool width: 930mm for roof panel
Rock wool thickness: 50~150mm
Polyurethane glue: A two-component adhesive is used, consisting of component A and component B. Mix two components and apply the mixture immediately to the panel after it turns black. Adhesive bond strength should be more than 10N/cm. Keep the adhesive clean and free of impurities. Foam rising time of component A after mixing is 20s to 40s. Curing time of component B is 50s to 70s after mixing.
Warranty Period and Installation
Guarantee period: one year for the complete sandwich panel production line
Installation, commissioning and training: We will send two engineers for free-of-charge on-site commissioning and training service.