Ceramic Foam Concrete Block, Insulation Board Production Line
Introduction:
The ceramic foam concrete block, insulation board production line can be used to produce lightweight ceramsite reinforced foam concrete block (panel). This material, adopting foam concrete and ceramsite as the supporting aggregate, is a kind of prefabricated material made of mixed foam concrete. This production line produces blocks or panels by molding and cutting.
The production line adopts advanced automatic mechanical cutting system and highly effective foaming technique which can effectively mix the lightweight ceramic with air entraining agent, so that the block can be more solid and flexible. The block also features good thermal insulation performance.
The ceramic foam concrete block, insulation board production line mainly consists of ceramic metering equipment, powder metering equipment, conveyor, mixing and injection molding machine, mold, cutting machine, stacking machine and packaging device etc.
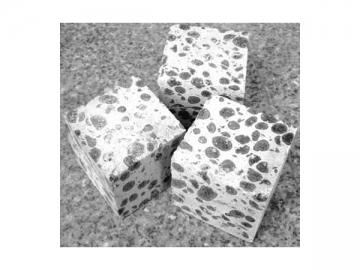
Introduction of the ceramsite reinforced foam concrete block:
The ceramsite reinforced foam concrete block takes ceramic as the aggregate and cement as the basic material. It is produced by batching, mixing, foaming, bubble mixing, molding and cutting. This block features good thermal insulation and lightweight.
This kind of concrete block is suitable for various buildings such as house, hotel, office building, school, factory, indoor thermal insulation for breeding industry. The construction can be quite simple. It only requires one-step forming with no need of secondary maintenance.
Intensity level | A3.5 | A5.0 | A7.5 | ≥7.5 | |
Compressive strength(Mpa) | Average value | ≥3.5 | ≥5.0 | ||
Minimum value | ≥2.8 | ≥4.0 | ≥6.0 | ||
Bulk density | B05 | B06 | B07 | ||
Dry bulk density kg/m3 | ≤550 | ≤650 | ≤750 | ≤800 | ≤800 |
Drying shrinkage | Rapid testing procedure | mm/m | ≤0.8 | ||
Standard testing method | ≤0.5 | ≤0.5 | ≤0.5 | 5.0 | |
Post freezing intensity Mpa≥ | 2.8 | 4.0 | 6.0 | ||
Heat conductivity coefficient(dry)W/m.k≤ | 0.12 | 0.14 | 0.16 |
Normal dimension of the block mm | Actual dimension of the block mm | ||||
Length L1 | Width B1 | Height H1 | Length L1 | Width B1 | Height H1 |
600 | 100 | 200/250/300 | L-10 | H-10 | |
125 | |||||
150 | |||||
200 | |||||
250 | |||||
300---120 | |||||
180 | |||||
240 |
Raw material: (shale, clay, coal ash, sludge etc.) ceramic, cement, coal ash, additive;
Unit weight: unit weight for 1 m3 product is 500-750kg;
Performance: no radioactivity, no hazardous substance, low shrinkage and colorful.
1. Lightweight
The dry bulk density of the ceramic reinforced foam concrete block is only 450~750 kg/m3, which is 1/3 that of the clay brick and 1/4 that of the concrete. So by adopting this kind of block, the weight of the building can be effectively reduced.
2. High intensity
The ceramic reinforced foam concrete block adopts the technology of ceramic reinforcement to satisfy the standard that the compressive strength of the nonbearing outer wall should be no less than 5.0MPa.
The testing of block hanging performance showed that when we adopt M10 connection elements, the depth of the anchor bolt is 70mm, the out extending length of the suspension point is 100mm and the suspension load is 1000N, the wall is undamaged within 24 hours. When the total load reached 1203N, the connection element bent while the wall was undamaged as well.
3. Thermal insulation
Heat conductivity coefficient of the ceramic reinforced foam concrete block is less than 0.16 W/m.k, which is 1/5 that of the clay brick and 1/8 that of the concrete. Just for the material, 200mm wall can perfect satisfy the requirements of energy-saving. By adjusting the wall thickness or some other matched energy-saving measures, we can easily realize the building design requirements of saving 65% of energy.
4. Fire proof
The raw material is inorganic and incombustible material which will not generate harmful gas under high temperature. According to the detection carried out by NFFE of Shanghai fire research institute of MPS, the unexposed surface temperature rise of the 120mm wall is only 42℃ after being exposed under 1200℃ for 4 hours, which is far lower than the national standard of less than 140℃.
5. Sound insulation
There are large amounts of pores inside the ceramic reinforced foam concrete block which functions as sound insulation and sound adsorbing. According to the testing results provided by the hotel, the sound insulating effect of the 120mm internal parting wall can completely meet the designing requirements of the 5-star hotel.
6. Precise dimension
This kind of block adopts automatic cutting machine, so that the dimension of the products can be quite precise. The dimension error can be controlled within ±1mm, so that it can effectively ensure the construction quality of the wall.