Two Colour Sandal Injection Moulding Machine, HB220Q/HB224Q
This sandal injection moulding machine is used to produce single-colour and two-colour foam or non-foam soles, sandals and slippers. All of these products can be made out of raw materials like TPR, PVC and PUR. In addition, this injection moulding machine is equipped with 24 sets of molds, meaning that as many as 12 pairs of shoes can be produced at a time.
Item | Unit | | |
Raw materials | TPR, PVC, PUR (blowing) | ||
Stations | 20 | 24 | |
Screw diameter | mm | 70 50 | |
Maximum injection volume | CC | 769 390 | |
Injection pressure | MPa | 70 | |
Clamping force | Tons | 80*2 | |
Yield | Pairs/hour | 80-150 | 100-200 |
Mould space | mm | 500*240*240 | |
Heating power | kW | 9 6.5 | |
Total power | kW | 50 | |
Dimensions | cm | 680×530×220 | 750×600×220 |
Machine weight | Tons | 11.6 | 12.8 |
Oil consumption | L | 600*2 |
-
V type mould structure
-
Mould manipulator
-
Energy-saving hydraulic servo control system
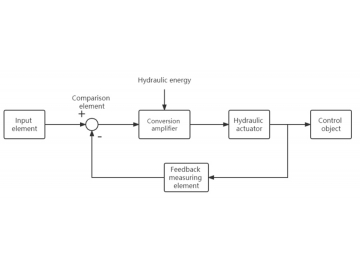
- Bonding of shoes’ different parts is achieved by non-adhesive technologies that feature excellent bonding performance;
- Screw rods are made through special techniques, ensuring exclusive durability;
- Block cylinder is made with an unique structure that is highly resistant to heat and leakage;
- Pre-heating system is optional to reduce defective rate;
-
Powerful air blowing system has been installed to realize efficient feeding of air, which helps make quality products with 30% less weight;
-
This injection moulding machine has a user-friendly PLC control system with industrial human-machine interface (HMI);
-
PLC control system
-
PLC
-
HMI interface
-
-
Servo motor and automatic mould manipulator are optional to save energy and reduce labour intensity;
-
To ensure operators' safety, multiple measures have been adopted, including:
-
Safety sign
-
Safety door with photoelectric switch
-
Safety door with photoelectric switch
-
Emergency stop button
-
Rotary table anti-lifting switch
-
To be specific, the safety sign will remind people of potentially dangerous zones; photoelectric switch can timely shut down the injection moulding machine to prevent operators accidentally reach out their hands into it; emergency stop button allows operators to shut down the injection moulding machine when finding something unusual happens; turn table anti-lift switch sends electric signals to shut down the injection moulding machine to prevent the turn table from being separated from the wheel.
Apart from these safety components, this injection press is equipped with other devices. Safety door is installed to allow operators to shut down the injection machine when malfunctions happen; safety net is set up to prevent misoperation.
-
Cooling tower is installed to bring down the temperature of hydraulic oil and raw materials;
-
Crusher is used to recycle used materials;
-
Vertical mixer blends materials with different colours and turn them into the same colour;
-
Air compressor will be connected to the injection moulding machine to supply air;
-
Drying system eliminates water in air so as to avoid bubbles in finished products and make better foam soles;
Parts list | ||
Toolbox | / | 1pc |
Allen key | 1.5-10 | 9 sets |
Open-end wrench | 6-24 | 8 sets |
Phillips screwdriver (small) | / | 2pcs |
Phillips screwdriver (large) | / | 1pc |
Adjustable wrench | 250mm | 1pc |
Heating ring | Ø120*80 mm | 1pcs |
Heating ring | Ø70*50 mm | 1pc |
Heating ring | Ø90*80 mm | 1pc |
Heating ring | Ø65*50 mm | 1pc |
Heating rod | Ø15.8*100 mm | 2pcs |
Proximity switch | Ø 25*25mm | 1pc |
Proximity switch | Ø 12*12mm | 1pc |
Thermoelectric coupling | K type/5M | 2pcs |
Oil seal | / | 2pcs |
Plugging rod | / | 1pc |
Plugging bushing | / | 1pc |
Copper gasket | / | 1pc |
Injection nozzle | / | 1pc |
User manual | / | 1 |