Low Cure Powder Coating
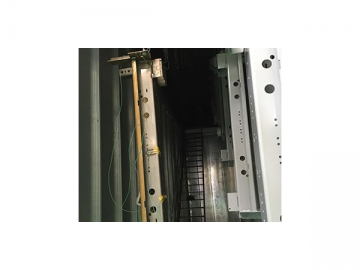
Before the workpiece is sprayed, the temperature tracker will move with it into the furnace and measure the temperature in 6 different spots.
Before the spraying process
At the spraying process
After the spraying process
On the market, common curing conditions of the low cure powder coating is 145°C at 20 minutes. Our product requires conditions of only 130°C for 20 minutes, while still possessing the same physical and chemical properties.
Important Advantages This powder coating significantly reduces energy consumption and improves the working environment.
Powder category: Epoxy polyester powder coating
Spraying method: Electrostatic spraying
Glossiness: 60-70
Specific gravity: 1.3-1.5g/cm3
Storage condition: <25℃, sealed in dry and cool place
Validity period: 6 months (<25℃)
Curing condition: 130℃*20minutes (temperature of workpiece)
A wrong curing condition fails to achieve the desired color, glossiness and coating property.
Testing condition: All chemical and physical property tests are conducted in labs under strict conditions. The above information and data is for reference only, and the final properties of the product depend on actual working environments.
Workpiece: Steel plate
Coating thickness: 60-80 μm
Curing condition: 130℃*20minites (temperature of steel plate)
Physical Properties
Appearance of coating (visual) | Uniform distribution of decorative pattern |
Coating thickness | 60~90μm |
Glossiness (60° light source) | Depending on demand |
Impact resistance (drop hammer) | 50kg (4.9Nm) pass |
Cupping test | >4mm |
Cross adhesion | 0 |
Surface hardness | 2H |
Salt spray test | 500hr. Pass |
Humidity resistance | 500hr. Pass |
Water immersion test | 240hr. Pass |
Acid resistance (5% HCL) | 240hr. Pass |
Alkali resistance (5%NaOH) | 240hr. Pass |
Chemical Properties
Humidity test(200h) | GB/T 1740-2007 GB/T 1766-2008 | 0degree |
Water resistance (23℃) 168h | GB/T 1733-1993(Method A) GB/T 1766-2008 | 0degree |
Gasoline resistance (25℃93#) 24h | GB/T 9274-1988(Method0degree A) GB/T 1766-2008 | 0degree |
Salt spray test (240h) | GB/T 1771-2007 GB/T 1766-2008 ISO 4628-8 2012 | Aging performance 0degree Corrosion extension along the cross line 0mm |
Salt spray test (48h) | GB/T 1771-2007 GB/T 1766-2008 ISO4628-8:2012 | There are no oxides, bubbles, peeling or coating softening outside the corrosion extension area. |
Main Features 1. Our plastic powder contains no toxins or volatile substances or solvents, ensuring the security.
2. We use recyclable powder supplied by trusted manufacturers, allowing us the highest utilization rate possible.
3. An easy and automatic operating method contributes to a high production efficiency and low cost.
4. The powder coating features a high density, excellent adhesion, excellent impact resistance, outstanding roughness, a large covering surface, and great corrosion resistance and electrical insulation capacity.
5. It is easy and convenient to store and transport our powder coatings.
Notes:
1. Powder coatings have a high standard for the working environment. The environment should have excellent ventilation and a temperature of less than 35°C.
2. The low cure powder coating should be stored in a cool, dry place, avoiding powder caking or solidification while spraying.
3. Our coating is 100% solid powder. Workers must take protective measures and wear protective clothing and avoid skin contact with the powder coating. If the skin does come into contact, was immediately with soap and water.
4. After the spraying process, the powder will be exposed to static electricity and create a coating layer on the workpiece in order to achieve the desired effect. The spraying device should be grounded, eliminating the static electricity from touching the device. By doing so, users ensure the entire coating and spraying process won’t be affected by static electricity.
If you are interested in our product, please click the "" to choose the color you want.