VCI Film Roll
VCI film roll is rolled into a tube shape or torn into a single layer and cut into a fixed VCI film sheet size and rolled only after the VCI film has extruded from the VCI film extrusion machine.
VCI film is often divided into VCI film rolls and VCI tubing rolls.
VCI film roll- Customers can cut VCI film sheets into different sizes and shapes.
VCI tubing roll- Customers can produce bags in a variety of sizes using VCI tubing rolls.
Adding an antistatic agent during VCI film production protects electronic components against static electricity.
Advantages:
-Effective corrosion protection and packaging combined in one step.
-VCI rust prevention sheeting protects different metal types, thus saving time, money, and resources.
-VCI film rolls are transparent, leading to an excellent visibility for packaged goods.
-VCI film rolls are easy to use: they are ready to apply right after taking them out of the package.
-VCI film rolls are environmentally friendly and recyclable.
Our VCI film roll types include standard VCI film rolls, heavy-duty VCI film rolls, VCI stretch film rolls and VCI tubing rolls.
Standard VCI film rollTechnical Parameters:
Thickness: 2μ~8μ
Width: ≤3m
We introduce an antistatic agent into the production process for VCI antistatic film rolls.
Standard VCI film rolls use polyethylene material as the base material, and VCI additives in different proportions using specialized extrusion equipment. This ensures the films have an excellent transparency, excellent barrier properties, a long service life, and are easy to use.
Applications: steel, copper, copper alloys and galvanized steel sheets; applicable in electronics, electrical engineering, instruments, micro motors, military industries and more
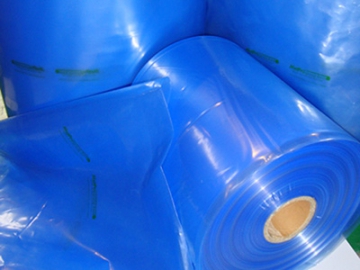
Technical Parameters:
Thickness: 2μ~10μ
Width≤3m;
We introduce an antistatic agent into the production process to produce enhanced VCI antistatic film rolls.
Heavy-duty VCI film rolls use polyethylene material as the base material, improving the physical strength, as well as guaranteeing the corrosion resistant performance. This gives the rust prevention sheeting a wider applicability range due to its improved structure.
Applications: coated and greased cold rolled sheets and color-coated sheets; applicable in rustproof packaging of larger and heavier metal products in mechanics, electromechanical industry and more.
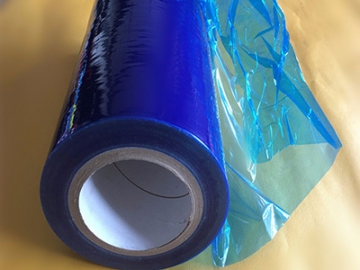
Technical Parameters:
Thickness: 0.9μ;
Width≤2m;
Standard: 1300m/roll
We can produce VCI stretch films with an antistatic agent.
VCI stretch films are applicable for the protection of polymetallic products against corrosion. VCI antistatic stretch films are applicable for protecting electronic components.
The stretch rate of VCI stretch films is 300%, and the films feature a single sided adhesion, corrosion resistance, and stretch wrapping, ensuring metals are fully packaged and sealed. When using VCI stretch films to package metals, VCI liquid will vaporize and protect said metals against corrosion by forming an invisible surface barrier.
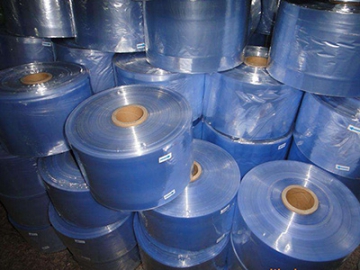
Technical Parameters:
Thickness: 2μ~10μ;
Width≤1.5m;
We add antistatic agents to the production of VCI antistatic films.
We produce VCI anti-corrosion films in a tube shape, then we weld the film into corrosion resistant bags of different sizes. VCI rolls can be turned into two bag types:
VCI flat bag
VCI gusseted bag
Cautions:
1. It is necessary to ensure that packaged products are clean and rust free, with no exposure to other corrosive chemical materials on the product surface before packaging.
2. During the packaging process, the temperature of packaged products and the surrounding environment should remain constant through the entire operation.
3. When packaged products are large-scale equipment, large box inner packaging or intensive products, we recommend using VCI material such as rust prevention paper, rust prevention bags, rust prevention powder and other rust prevention materials.
4. No barrier should exist between the packaged products and the rust prevention paper, such as a paper pad, protective bag or plastic board. It should also be noted that other paper types and wooden material should not come into direct contact with the packaged products.
5. Users wear gloves through the entire operation process in order to prevent corrosion caused by sweat or other skin oils.
6. The packaging antirust paper should not remain exposed to open air for long periods of time before use. After packaging, the packaging container should be sealed as soon as possible using a heat seal, adhesive tape, or cable tie. Any remaining anti-rust paper should be resealed in an enclosed space.