Fully Automatic Single Sachet Wet Wipes Multiple Packaging Machine
DC-22 Wet Wipes Machine (1 pc/pack)
Wet wipes machine integrating folding, wetting, stacking, packaging and sealing
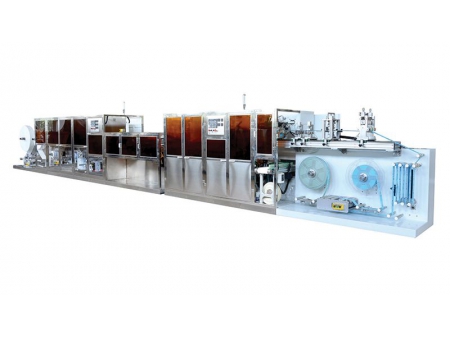
- Production Speed 350-500 wipes per minute
- Design Speed 50 packs per minute
- Package Quantity 5-10 individual sachets per pack
This fully automatic single sachet wet wipes packaging machine combines high efficiency with intelligent features to streamline your wet wipes production. Equipped with automatic reject mechanism, it automatically detects and rejects empty or incorrectly cut pouches, ensuring perfect packaging every time.
The wet wipes machine also offers automatic counting and stacking, with customizable stack sizes ranging from 5-10 pieces per stack. Vacuum suction cups ensure reliable bag handling, while servo motors transport the pouches to the positioning mechanism, making operation quick and seamless. With both manual and automatic modes available, this sachet wet wipe machine adapts to your production needs.
The suspended touchscreen control panel is highly intuitive, and each motor can be individually controlled, offering flexibility and ease of use. It’s the ideal solution for businesses seeking efficient, precise, and intelligent wet wipe packaging.
Production speed | 30-40 packs/min |
Design speed | 50 packs/min |
Quantity per pack | 5-10 individual sachets /pack |
Defective rate | ≤2% |
Voltage | 380V 50HZ |
Power | Approx. 20kW |
Machine dimensions (L×W×H) | 4000×1400×1650mm |
Bucket package | Customizable |
- The wet wipe is automatically pushed into the pre-formed bag by the servo bag filling mechanism, while simultaneously delivering the bag and product to the hot sealing unit.
- Utilizes a servo motor drive system, providing high precision and stability for smooth and reliable operation.
- Offers both automatic and manual modes, allowing flexibility in production process control.
- The suspended, rotatable touchscreen control panel allows operators to stand while quickly and accurately adjusting the machine settings.
- Each motor can be independently turned on or off, offering flexibility to adjust its operational status based on production needs.
- Two emergency stop buttons are strategically placed along its length to enhance safety and improve ease of operation.