DRY-2009 Semi-automatic Pulp Molding Machine
Description
DRY-2009 semi-automatic pulp molding machine is one of the most popular pulp molding machine in the world because of the low investment. However, this machine is suitable for those countries with cheap labor since every set of machine need manually operated. If you can obtain cheap labor and open a factory with low investment, it will be a good choice.
Application
DRY-2009 semi-automatic pulp molding machine can be used in the food packaging products which used plant fiber as raw materials (sugarcane, bamboo, wheat straw, reed, wood ). Those products including the plate, bowl, lunch boxes, supermarket tray and a variety of drinks cup, coffee cup, etc. It can be used in microwave oven, oven baked food, frozen and distillation food, besides it can also used for industrial packaging and commodities.
- Plate
- Bowl
- Box
- Tray
- Cup
- Slipper
Production process analysis
The production line of the DRY-2009 semi-automatic pulp molding machine is composed of five main processes: pulping, forming, modeling, cutting edge disinfection and finished packaging. See the process flowchart below.
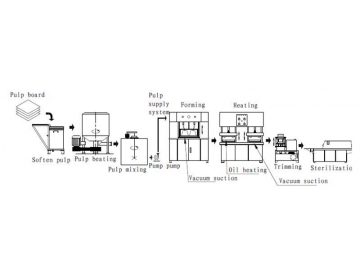
1. The pulping process is to make the quantitatively soaked pulp plate into paper pulp. The first step is finished by hydraulic pulping machine and let the pulp into the tank, adding edible grade waterproofing and anti-oil additives, and then into the pool. Secondly, the pulp is send to the automatic molding machine for precise quantitative grouting, and then use the hydraulic stir mix the pulp, then vacuum dehydration. Advanced technologies are used in the modeling process to eliminate perforation, uneven thickness and reduced waste. Finally, after modeling, those tableware are manually transferred to the thermostatic solidified mold for dehydration and solidification.
2. The modeling process adopts the patent technology ZL 2008 20101990.8. Compared to the traditional heating device, it can reduced 70% electric consumption and 30% production cost. The process meet the hygienic requirement of food packaging , it not only improve the energy utilization efficiency, but also ensure high yield and high quality, with a yield rate of more than 98%.
3. The molded semi-finished product will be transferred for cutting edge finishing and inspected to meet the factory requirement, disinfection and packaging into the warehouse.
Technical SpecificationItem | Technical data | Notes |
Dimension | 2060*820*2735mm (forming machine) 1665*1040*2170 mm (modeling machine) | Manufacture provide |
Weight | 2.63T (forming machine)/1.63T (modeling machine) | Manufacture provide |
Size | 750*600mm | Manufacture provide |
Capacity | 0.125KW | |
Circulation time | 60s | calculate use standard 10 inch disk (20g) |
Range | ±1.5g-5g | Product standard weight ±1.5-5 g |
Maxium power | 120KW | Manufacture provide |
Height | ≦100 mm | |
Daily capacity | 250KG (12500) | calculate use standard 10 inch disk (20g) |
Yield | ≧95% |
Production line features
1. All parts of the machine which contact the pulps including pipes and valves all made of stainless steel, and therefore have good resistance to corrosion and heat.
2. The mold of the forming machine and molding machine both use the alloy copper or (7075 alloy aluminum) material with high thermal conductivity, high abrasion resistance and high strength and high conductivity.
3. Steam and oil can all be used for heating which are more energy saving. Compared to the traditional heating device, it can reduced 70% electric consumption and 30% production cost.
4. The pressure-forming pressurized method adopts the Germany energy saving and pneumatic supercharging system. The high pressure make the product more dense and the operation is simple and the maintenance is convenient.
5. Adopted automatic weight control device and using the stainless steel double vacuum dehydrator is used for pulp, water seal operation and circulation. No sewage discharge and the utilization of materials almost 98%. The product has stable weight, uniform thickness and 99% yield.
6. The product has stable weight, uniform thickness and 98% quality passing rate
7. Our company has passed the ISO9000, ISO14000 international management system qualification, and the sanitary requirements comply with FDA, SGS, BPI and international standard.