Magnetic Separator
Magnetic separator is widely used for separation of wet and strong magnetic minerals. The magnetic system adopted is made of high magnetic-energy and high-coercivity NdFeB magnet, which contributes to high magnetic field intensity and large effective depth. Demagnetization rate of the magnetic filed in 8 years is less than 5%. With a large wrap angle, the magnetic system ensures gradient increase and smooth transition of filed intensity. It enlarges the length of separation zone and enhances magnetic turning efficiency. Therefore, magnetic minerals can be efficiently separated from weak magnetic or non-magnetic minerals. The magnetic system is wrapped with a kind of material which is un-conductive magnetic and stainless, thereby efficiently preventing the magnet from falling off. The separator barrel is also un-conductive magnetic and stainless and it is also coated with corrosion-resistant rubber. Consequently, the service time of the barrel is extended.
Generally, the cell body is semi-countercurrent type. However, we still provide concurrent cell body if required. Both the magnetic system and the cell body can be customized according to customers’ requirements. Our magnetic separator is applicable for different environment. It is able to work normally even when ore quantity, feed size or pulp density changes significantly.
Based on the foundation structure, magnetic separator can be divided into concurrent type, countercurrent type and semi-countercurrent type.
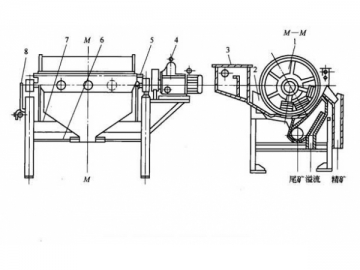
Structure of Concurrent Magnetic Separator
1. barrel
2. cell body
3. feeding box
4. transmission component
5. discharge pipe
6. regulating value for ore discharge
7. rack
8.steering gear
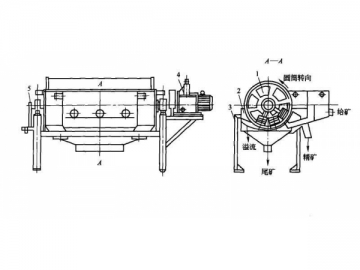
Structure of Countercurrent Magnetic Separator
1. barrel
2. cell body
3. rack
4. transmission component
5. steering gear
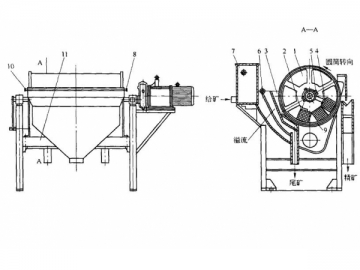
Structure of Semi-Countercurrent Magnetic Separator
1. barrel
2. magnetic system
3. cell body
4. magnetic guide plate
5. rack
6. spray pipe
7. feeding box
8. discharge pipe
9. foundation
10. adjusting device for magnetic declination
11. rack
1.
CTBY magnetic separator for preliminary beneficiation is used for wet pre-concentration of magnetite which has already went through fine grinding before and will enter the mill after pre-concentration. The feed size should be smaller than 10mm.
Model | CTBy1018 | CTBy1024 | CTBy1030 | CTBY1218 | CTBY1224 | CTBY1230 |
Barrel Diameter (mm) | 1000 | 1000 | 1000 | 1200 | 1200 | 1200 |
Barrel Length (mm) | 1800 | 2400 | 3000 | 1800 | 2400 | 3000 |
Filed Intensity of Barrel Surface (mT) | 350 ~ 550 | 350 ~ 550 | 350 ~ 550 | 350 ~ 550 | 350 ~ 550 | 350 ~ 550 |
Rotating Speed of Barrel (r/min) | 23 | 23 | 23 | 20 | 20 | 20 |
Capacity for Dry Ore (t/h) | 42 ~ 65 | 53 ~ 86 | 82 ~ 124 | 58 ~ 97 | 71 ~ 120 | 103 ~ 158 |
Feed Size (mm) | 0 ~ 10 | 0 ~ 10 | 0 ~ 10 | 0 ~ 10 | 0 ~ 10 | 0 ~ 10 |
Pulp Density (%) | 20 ~ 50 | 20 ~ 50 | 20 ~ 50 | 20 ~ 50 | 20 ~ 50 | 20 ~ 50 |
Motor Power (KW) | 5.5 | 7.5 | 7.5 | 7.5 | 11 | 11 |
Total Weight (t) | 5.2 | 6.4 | 7.1 | 6.7 | 7.2 | 8.9 |
Separator Length (mm) | 3160 | 3790 | 4460 | 3380 | 4190 | 4770 |
Separator Width (mm) | 2250 | 2250 | 2250 | 2460 | 2460 | 2460 |
Separator Height (mm) | 1750 | 1750 | 1750 | 2000 | 2000 | 2000 |
2.
CTBC magnetic separator for roughing is suitable for rough concentration of magnetite after one-stage grinding or multi-stage grinding. It also can be used for roughing during recovery of magnetic minerals from the tailings obtained after separation of non-ferrous metals. The feed size should be smaller than 4mm.
Model | CTBC1018 | CTBC1024 | CTBC1030 | CTBC1218 | CTBC1224 | CTBC1230 |
Barrel Diameter (mm) | 1000 | 1000 | 1000 | 1200 | 1200 | 1200 |
Barrel Length (mm) | 1800 | 2400 | 3000 | 1800 | 2400 | 3000 |
Filed Intensity of Barrel Surface (mT) | 300 ~ 500 | 300 ~ 500 | 300 ~ 500 | 300 ~ 500 | 300 ~ 500 | 300 ~ 500 |
Rotating Speed of Barrel (r/min) | 23 | 23 | 23 | 20 | 20 | 20 |
Capacity for Dry Ore (t/h) | 36 ~ 54 | 44 ~ 75 | 66 ~ 103 | 47 ~ 82 | 62 ~ 105 | 83 ~ 129 |
Feed Size (mm) | 0 ~ 4 | 0 ~ 4 | 0 ~ 4 | 0 ~ 4 | 0 ~ 4 | 0 ~ 4 |
Pulp Density (%) | 20 ~ 50 | 20 ~ 50 | 20 ~ 50 | 20 ~ 50 | 20 ~ 50 | 20 ~ 50 |
Motor Power (KW) | 5.5 | 7.5 | 7.5 | 7.5 | 11 | 11 |
Total Weight (t) | 5.2 | 6.4 | 7.1 | 6.7 | 7.2 | 8.9 |
Separator Length (mm) | 3160 | 3790 | 4460 | 3380 | 4190 | 4770 |
Separator Width (mm) | 2250 | 2250 | 2250 | 2460 | 2460 | 2460 |
Separator Height (mm) | 1750 | 1750 | 1750 | 2000 | 2000 | 2000 |
3.
CTBJ series magnetic separator for fine separation is suitable for further concentration of coarse concentrate which has already went through grinding and roughing before. The feed size should be smaller than 2mm.
Model | ||||||
Barrel Diameter (mm) | 1000 | 1000 | 1000 | 1200 | 1200 | 1200 |
Barrel Length (mm) | 1800 | 2400 | 3000 | 1800 | 2400 | 3000 |
Filed Intensity of Barrel Surface (mT) | 200 ~ 300 | 200 ~ 300 | 200 ~ 300 | 200 ~ 300 | 200 ~ 300 | 200 ~ 300 |
Rotating Speed of Barrel (r/min) | 23 | 23 | 23 | 20 | 20 | 20 |
Capacity for Dry Ore (t/h) | 24 ~ 36 | 33 ~ 56 | 46 ~ 72 | 35 ~ 45 | 43 ~ 77 | 54 ~ 86 |
Feed Size (mm) | 0 ~ 2 | 0 ~ 2 | 0 ~ 2 | 0 ~ 2 | 0 ~ 2 | 0 ~ 2 |
Pulp Density (%) | 20 ~ 50 | 20 ~ 50 | 20 ~ 50 | 20 ~ 50 | 20 ~ 50 | 20 ~ 50 |
Motor Power (KW) | 5.5 | 7.5 | 7.5 | 7.5 | 11 | 11 |
Total Weight (t) | 5.2 | 6.4 | 7.1 | 6.7 | 7.2 | 8.9 |
Separator Length (mm) | 3160 | 3790 | 4460 | 3380 | 4190 | 4770 |
Separator Width (mm) | 2250 | 2250 | 2250 | 2460 | 2460 | 2460 |
Separator Height (mm) | 1750 | 1750 | 1750 | 2000 | 2000 | 2000 |
4.
After grinding of magnetite, returning aggregates and magnetite concentrate will be obtained. CTBN magnetic separator is applicable for concentration of returning aggregates before entering the mill and concentration of magnetite concentrate before entering the filter in the next procedure. The feed size should be less than 4mm.
Model | ||||||
Barrel Diameter (mm) | 1000 | 1000 | 1000 | 1200 | 1200 | 1200 |
Barrel Length (mm) | 1800 | 2400 | 3000 | 1800 | 2400 | 3000 |
Filed Intensity of Barrel Surface (mT) | 260 ~ 450 | 260 ~ 450 | 260 ~ 450 | 260 ~ 450 | 260 ~ 450 | 260 ~ 450 |
Rotating Speed of Barrel (r/min) | 23 | 23 | 23 | 20 | 20 | 20 |
Capacity for Dry Ore (t/h) | 35 ~ 68 | 46 ~ 86 | 67 ~ 126 | 52 ~ 90 | 77 ~ 126 | 90 ~ 160 |
Feed Size (mm) | 0 ~ 4 | 0 ~ 4 | 0 ~ 4 | 0 ~ 4 | 0 ~ 4 | 0 ~ 4 |
Pulp Density (%) | 20 ~ 50 | 20 ~ 50 | 20 ~ 50 | 20 ~ 50 | 20 ~ 50 | 20 ~ 50 |
Motor Power (KW) | 5.5 | 7.5 | 7.5 | 7.5 | 11 | 11 |
Total Weight (t) | 5.2 | 6.4 | 7.1 | 6.7 | 7.2 | 8.9 |
Separator Length (mm) | 3160 | 3790 | 4460 | 3380 | 4190 | 4770 |
Separator Width (mm) | 2250 | 2250 | 2250 | 2460 | 2460 | 2460 |
Separator Height (mm) | 1750 | 1750 | 1750 | 2000 | 2000 | 2000 |