Rotary Screen Printing (2188 Series Textile Printing Machine)
2188 series textile printing machine is composed of four units, including fabric in-feed system, printing unit, drying unit and doffing unit. And these four units are driven by four servo motors.
2188 series textile printing machine consists of an enclosed foundation, scraper and coaxial transmission system (or independent transmission system).
-
Printing Example
-
Machine Detail
Machine Detail
Application
The 2188 series textile printing machine is quite suitable to print natural fibers, chemical fibers and synthetic fibers – woven fabric and knitted fabric.
Specifications of Rotary Screen Printing Machine
Application | Printing on natural fabrics, chemical fabrics, knitted fabrics and woven fabrics. |
Fabric weight | 50g/m2 to 600g/m2 |
Printing width | 1620mm(180 model) 1850mm (200 model) 2050mm (220 model) 2200mm (240 model) 2400mm (260 model) 2600mm (280 model) 2800mm (300 model) 3000mm (320 model) |
Printing colors | 8 color printing 10 color printing 12 color printing 14 color printing 16 color printing 20 color printing 24 color printing |
Repeat size | 640mm 820mm 914mm 1018mm |
Printing speed | 4-80m/min |
Type of screen head driving | Mechanical driving / individual driving |
Registering accuracy | ± 0.1mm |
Registering adjustment range | Vertical: Unlimited, horizontal: ± 10mm, diagonal: ± 3mm |
Drying method | Three layer, four outlet, hot air drying system |
Chamber of the dryer | 2-7 chambers, tighten or loose type |
Heat source for drying | Vapor / hot oil / fuel gas |
Fabric-entry and fabric-exit model | Open-width |
Machine type | Left hand type / Right hand type |
Compressed air pressure | 0.6-0.8Mpa |
Water pressure | ≥0.3Mpa |
Configurations | Fabric feeding device, printing system, drying system and doffing device. |
Product features
1. 2188 series textile printing machine’s working principle: Doctor blade is adopted to push the print paste through the design area of the screen onto the fabric.
2. The textile printing machine enjoys a large production capacity, which allows for a printing speed of 80m/min under normal circumstances.
3. JL2188 Series textile printing machine has a closed screen holder, and the rotary screen printing is driven by direct drive servo motors. The driving method allows for a higher printing precision.
4. As to registration control system, an embedded programmable logic controller is adopted on our JL2188 Series textile printing machine, which enables an intelligent registration.
Major components of JL2188 Series textile printing machine
Fabric in-feed system
Fabric in-feed system of JL2188 Series textile printing machine is composed of a frame ( bended steel plate), cloth guider (or a simple alignment tool), tensioner, pinch rolls, vacuum cleaner, pressure regulator, automatic alignment tool, cloth guide roller and etc.
Thanks to fabric feed-in device, the tensile force could be well adjusted according to fabric’s materials, which helps to provide precise straight feeding of the textile fabric onto the textile printing machine.
Printing Unit
Independent transmission: Guiding belt is activated by main transmission motor, and the printing head is driven independently by direct drive servo motor. And the simultaneous printing could be achieved with the help of computer.
The alignment of guiding belt is in well accordance with the principle of three-roll alignment, and the pendulum angle of controlling roll is determined by electric motor. And at the same time, there are two switches to control the direction and the operation of electric motor. And the switches’ mode (on /off) is driven by a roller, which is installed closely to the edge of guiding belt.
Therefore, if the guiding belt is installed correctly and trimmed well, the textile printing machine will have a smooth operation and its allowable tolerance is under ±3mm.
1. Two transmission driving methods: coaxial transmission system (group driving) or independent transmission
2. Pump: The pump is of stainless steel structure, and its controlling mode could either be manual control or automatic control. The automatic control is achieved by liquid level control and programmable logic controller.
3. Guiding belt washing system: After one-shot printing, the guiding belt would be adhered with some dirt, such as waste cotton, glues, ink paste and etc. The dirt needs to be washed off before the next run of printing. Guiding belt washing system is composed of two parts: pre-washing and main washing.
Pre-washing: During pre-washing, shower pipe and sponge will be adopted. The process could help to clean most of the waste cotton, ink pastes and etc.
Main washing: During the process, four show pipes, two foam sponges, and three rubber doctor blades will be arranged at regular intervals. These cleaning devices will used to flush, scrape, wipe, wash and dry the guiding belts repeatedly.
4. Appliqueing system: Water-soluble adhesive bonding; adhesive bonding of thermoplastic material for doctor blade, bonding forφ20magnetic bar and thermoplastic material
5. Adhesive removing device: Cooper scraper
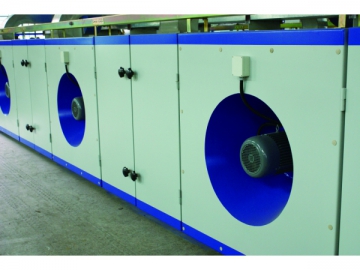
Drying System
Drying system: multi-layer heat drying system, and three-layer structure for cloth placing. Its capacity is determined by the number of drying chamber.
1. Its frame is made of structural steels and its thermal insulation board and door are all of hollow structure with mineral wools inside. Meanwhile, its radiator fin adopts quality cooled rolled aluminum plates as its raw material. After assembly, the drying unit will undergo an extra treatment –silver powder spraying. Since silver powers are thermal resistant, the sprayed drying unit also features good performance in thermal conductivity and corrosion resistance.
2. Circulating fans are installed on both sides of the drying rooms, and its wind speed arrives to 22m/s in its vent. Meanwhile, the fan blades of circulating fan are made of aluminum alloy. Besides that, we also optimized the overall design of drying room – installing the thermal insulation devices, which enables a 40% lower of installed power when compared with that of traditional drying room.
3. Exhaust fan is installed on the top of drying room.
4. Conveyor belt is a PTFE coated woven belt, which is highly thermal resistant. When it is activated, the conveyor belt will be under alignment with the help of two coated rollers. These two rollers are installed on its swing arms.
Doffing system: frame, cloth guide roller, pressure regulator, swing arm and etc.
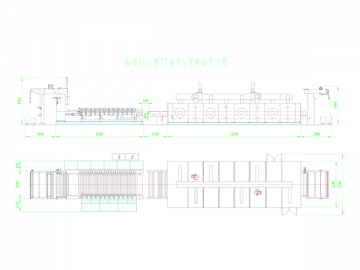
How to choose a textile printing machine?
1. Check fiber material: woven fabric, knitted fabric or both.
2. Check the maximum efficient breadth of printing
3. Check the maximum number of overlapping colors
4. Available drying house:
4.1 Compact- type drying room for woven fabric
4.2 Loose-type drying room for knitted fabric, and installing an overfeed device on its heat pump
4.3 Loose-type drying room for both woven fabric and knitted fabric, and installing an overfeed device on its heat pump
4.4 Standard drying room has 4 chambers, and chamber’s number could be changed according to customers’ requirement.
4.5 Check the heat source: steam, heat transfer oils or fuel gas (natural gas, coal gas)
5. Plan sketch
5.1 Standard in-feed system, woven fabric and compact-type drying chamber
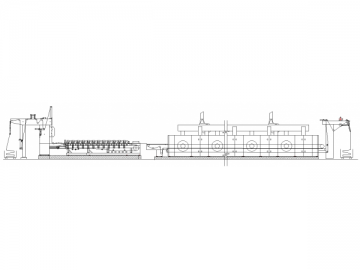
5.2 Standard in-feed system, woven fabric and loose-type drying chamber
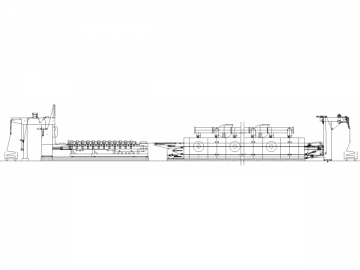
5.3 Standard separated in-feed system, woven fabric, and compact-type chamber
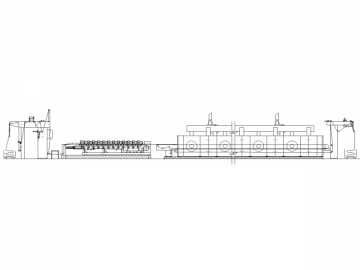
5.4 Standard separated in-feed system, woven and knitted fabric, loose-type drying room

5.5 Double-duty in-feed system, woven and knitted fabric, loose-type drying room
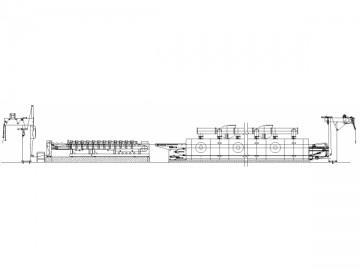
5.6 Standard separated in-feed system, woven and knitted fabric, elevated loose-type drying room
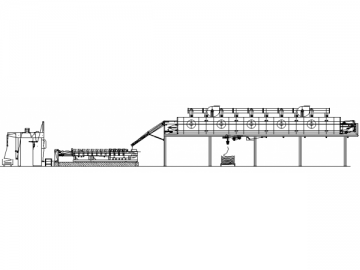
As a traditional rotary screen printing machine, JL2188 Series textile printing machine has been sold in China for two dozen years. And now, it has become a quite mature product in China’s textile printing market, which enjoys high market share, easy operation and mature manufacturing technology.