Honeycomb Ceramic
Honeycomb Monolith / Porous Ceramic / Ceramic Block
Honeycomb ceramic is a porous ceramic with parallel channels that are triangular, square or hexagonal in shape. Each honeycomb unit is separated by thin walls, and materials making up the ceramic honeycomb primarily include cordierite (2MgO.2Al2O3.5SiO2), aluminum titanate (Al2TiO5), mullite (3Al2O3.2SiO2), Corundum (α-Al2O3) and compound phases.
Compared to general ceramics, the honeycomb ceramics feature a low thermal expansion, high heat and shock resistance, anti-oxidation performance, a large surface area and corrosion resistance.
Applications
Honeycomb ceramics are used in metallurgy, tower packing in the chemical industry, construction, heat regenerative and high temperature air purification, industrial waste gas treatment, NOx purified systems in firepower, purifying systems for harmful gasses from burning refuse, noxious gas purification in chemical and mining industries, and finally, acting as a filter and catalyst carrier used in founding processes. Honeycomb ceramic regenerators enhance efficiency, save energy, increase output, and improve the quality, all important and effective measures to take when handling energy and the environment. These ceramic tools are also used to save energy on thermal equipment. Pores inside the honeycomb ceramic regenerators are square and hexagon in shape, and each channel is straight and parallel to each other. This unique structure reduces the passing air resistance and enhances the heat exchange efficiency of every channel.
Functions
1. Reduce the thermal loss in exhaust gas, and improve the efficiency of fuel in order to save energy
2. Enhance the burning temperature based on theory, and improve atmospheric burning to meet the high temperature requirements of thermal equipment to enlarge the caloric value of fuel, especially when used in blast furnaces. The ceramic product is also used to improve the calorific value of fuel and reduce emissions from low calorific value coal gas.
3. Improve the heat exchange in hearths, increase equipment output, and enhance the quality of products to cut down on equipment reinvestment costs.
4. Reduce exhaust emissions in thermal equipment, alleviate air pollution, and improve the environment
Size
150*150*300mm
150*150*150mm
100*100*100mm
150*150*100mm
from 13 cells, 25cells, 32cells 40cells, 50cells, 60cells to 400cpsi
Materials
Micrographs of ceramic material
Poro cordierite
Dense Cordierite
Porcelain
Dense alumina
Mullite
Corundum Muillte
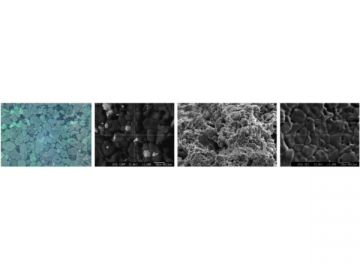
Chemical analysis
Composition | Value (%) |
Al2O3 | 55~65 |
SiO2 | 25~35 |
MgO | 1~5 |
Fe2O3 TiO2 | 3~5 |
Others | <5 |
Index | Unit | Value |
Density | g/cm3 | 2.0±0.2 |
Coefficient of heat expansion | ( X10-6K-1) ( 20-800℃ ) | ≤5 |
Specific Heat | ( J/Kg.k ) ( 20 ~ 1000℃ ) | 900-1150 |
Thermal Conductivity | ( 20 ~ 1000℃ ) | 1.5 ~ 2.0 |
Impact Thermal Resistance | ( ℃/min ) | ≥300 |
Max. Working Temp. | ℃ | 1350 |
Water absorption | % | ≤20 |
Dimension | Quantity of channels | Wall thickness | Outside wall thickness | Channel Width | Void section | Weight piece |
150×150×300 | 25×25 | 1.0mm±0.1 | 1.2mm±0.15 | 4.8-5.0mm | 67% | 4.0-5.0kg |
150×150×300 | 32×32 | 0.9mm±0.1 | 1.2mm±0.15 | 3.8-3.9mm | 61.6% | 4.6-5.6kg |
150×150×300 | 40×40 | 0.7mm±0.1 | 1.1mm±0.15 | 2.9-3.1mm | 64% | 4.7-5.7kg |
150×150×300 | 43×43 | 0.65mm±0.1 | 1.1mm±0.15 | 2.7-2.9mm | 62% | 4.8-5.8kg |
150×150×300 | 50×50 | 0.6mm±0.1 | 0.8mm±0.15 | 2.3-2.5mm | 61% | 4.8-5.8kg |
150×150×300 | 60×60 | 0.45mm±0.1 | 0.8mm±0.15 | 1.9-2.1mm | 63.4% | 4.7-5.7kg |
Due to the reliable quality and economic price, we export honeycomb ceramics all over the world to Germany, USA, Japan, South Korea, Philippines, Italy, France, Saudi Arab, Iran, Brazil, Morocco, Chile and other places. We are also working on a number of RTO projects for honeycomb media and insulation materials, so that we can always ensure the best services.