Medium Frequency Induction Melting Furnace
Introduction and Applications:
The medium frequency induction melting furnace is a device that converts three phase power current into single phase intermediate frequency current and enables metal to produce eddy current loss through EMF induction. This process allows the equipment to perform heating, melting and holding functions for steel, copper, aluminum, zinc, tin, nickel, silver and other metals and alloys. You can also use this furnace for heat treatments prior to forging, sintering and tube bending in casting and other metal processing industries.
-
Medium frequency induction melting furnace The steel shell furnace is pouring the liquid Steel shell furnace Aluminum shell furnace
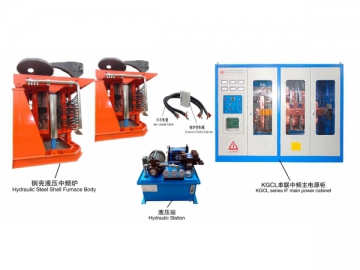
Performances and Features:
1. Zero-voltage scanning soft start, start or stop at any time under any state without impact on power supply.
2. Speedy melting, low production cost, low pollution, conforms to environmental protection requirements.
3. Direct melting starting from low temperatures, available for fully empty ing of solutions, easy change of category of melting material.
4. Flexibly adjustable power, easy and continuous smooth adjustment, easily controllable temperature, low oxidization loss, uniform metal content.
5. Furnace shell with cast aluminum alloy or steel shell construction, available for selection of electric, manual, hydraulic or other overturn modes as needed.
6. Complete set of equipment can realize fully automatic remote control. It includes PLC (Programmable Logic Controller), HMI (Human Machine Interface) or industrial control system, industrial control configuration software and various sensors etc. The use of automatic constant-temperature control function, automatic heating lining function, oven anti-leakage alarming function and other functions makes this equipment safe and easy to use.
Automatic Constant Temperature Control Function:
You can pre-set the temperature range of water. The constant temperature can be realized by a single button. Compared to traditional manual temperature control, the automatic control saves time and labor. In addition, it is more sensitive and more accurate. The water temperature is easier to control resulting in less oxidation loss, more uniform casting and better finished product quality.
Automatic Heating Lining Function:
Heating lining is a relatively complicated and long process of the temperature rise curve, to extend the service life of the intermediate frequency furnace. The one-click start, automatic matching and stepless regulation of intermediate frequency power, the size of the control of heating speed, prevent lining cracks, and achieve the goal of automatic lining curve. This helps to avoid misoperation and at the same time reduce the labor time and intensity of the workers.
Oven Anti-Leakage Alarming Function:
Working Principal: With the use of the furnace, the furnace wall will become thinner and thinner during use. IF current will change according to the furnace wall. If the current reaches a preset value, the alarm system will ring and automatically cut off power.
Two furnaces can be connected in series to a power supply. With the rotary switch or the digital operating screen, you can adjust the power distribution of the two furnaces. The total power of the power supply can be distributed at will to two furnaces, so that a furnace can melt the metals while another can maintain its temperature. This mode greatly improves the production capacity and saves energy.
Model Capacity | Power input (50/60HZ) | Power output | Melting time (min) | Power consumption (KW H/T) | ||||||||||
Rated power (KW) | Input voltage (V) | Input current (A) | Pulse number of rectifier | Capacity of rectifier transformer (KVA) | DC voltage (V) | DC current (A) | Medium Frequency voltage (V) | Frequency K HZ | Cast iron | Red copper | Brass | Aluminum | ||
GW--0.05T | 50 | 380 | 80 | 6 | Three phase 50 | 500 | 100 | 750 | 1 | 20- 40 | 7 50 | 51 0 | 4 7 0 | 65 0 |
GW--0.1T | 100 | 380 | 160 | 6 | Three phase 100 | 500 | 200 | 750 | 1 | 20- 40 | 7 00 | 51 0 | 4 7 0 | 64 0 |
GW--0.15T | 1 6 0 | 380 | 256 | 6 | Three phase 200 | 500 | 320 | 750 | 1 | 2 0- 40 | 6 50 | 50 0 | 43 0 | 63 0 |
GW--0.25T | 200 | 380 | 320 | 6 | Three phase 250 | 500 | 400 | 750 | 1 | 2 0- 45 | 6 50 | 50 0 | 42 0 | 61 0 |
GW--0.35T | 250 | 380 | 400 | 6 | Three phase 315 | 500 | 500 | 750 | 1 | 2 0- 45 | 65 0 | 4 9 0 | 41 0 | 60 0 |
GW--0.5T | 350 | 380 | 56 0 | 6 | Three phase 400 | 500 | 7 00 | 750 | 0.8 | 30- 50 | 6 3 0 | 4 8 0 | 40 0 | 57 0 |
GW--0.75T | 5 00 | 380 | 80 0 | 6 | Three phase 630 | 500 | 10 00 | 750 | 0.8 | 40- 5 0 | 6 2 0 | 4 7 0 | 39 0 | 56 0 |
GW--1T | 8 00 | 380 | 128 0 | 6 | Three phase 1000 | 500 | 1 6 00 | 750 | 0.7 | 40- 5 0 | 6 2 0 | 46 0 | 38 0 | 55 0 |
750 | 656 | 6 | Three phase 1000 | 990 | 808 | 14 8 0 | ||||||||
GW--1.5T | 10 00 | 380 | 800 | 12 | Dual three phase 1250 | 500 | 10 00 | 750 | 0.7 | 40 - 6 0 | 60 0 | 45 0 | 37 0 | 54 0 |
750 | 820 | 6 | Three phase 1250 | 990 | 1010 | 14 8 0 | ||||||||
GW--2T | 1 40 0 | 750 | 1148 | 6 | Three phase 1800 | 990 | 1414 | 14 8 0 | 0.5 | 45 - 6 0 | 60 0 | 44 0 | 3 6 0 | 53 0 |
75 0 | 574 | 12 | Dual three phase 1800 | 990 | 707 | 1480 | ||||||||
GW--3T | 20 00 | 75 0 | 820 | 12 | Dual three phase 2500 | 990 | 1010 | 1480 | 0.5 | 50- 7 0 | 58 0 | 430 | 3 5 0 | 52 0 |
GW--5T | 30 00 | 95 0 | 1140 | 12 | Dual three phase 4000 | 1 260 | 1190 | 1 90 0 | 0.3 | 5 0- 8 0 | 5 7 0 | 42 0 | 34 0 | 51 0 |
GW--10T | 6 000 | 95 0 | 2280 | 12 | Dual three phase 8000 | 1260 | 2380 | 1 90 0 | 0.3 | 5 0- 9 0 | 5 6 0 | 41 0 | 33 0 | 49 0 |
GW--15T | 8 000 | 95 0 | 1520 | 24 | Quadruple three phase 10000 | 1 260 | 1590 | 1 90 0 | 0.3 | 5 0- 9 0 | 550 | 400 | 320 | 480 |
GW--20T | 10000 | 950 | 1900 | 24 | Quadruple three phase 12500 | 1260 | 1980 | 1 90 0 | 0.25 | 5 0- 9 0 | 530 | 400 | 310 | 470 |
GW--30T | 15000 | 950 | 2850 | 24 | Quadruple three phase 20000 | 1 260 | 2980 | 1 90 0 | 0 . 25 | 5 0- 9 0 | 520 | 400 | 310 | 450 |
Temperature in furnace: Steel 1650 ℃; Cast iron 1450 ℃; Red copper 1150 ℃; Brass 1000 ℃; Aluminum 700 ℃; Zinc 400 ℃ |
※ Furnace capacity is calculated on the base of steel with density of 7.8
※ Melting time and power consumption is important to equipment power, raw material shape and weight, operator’s skill level and other elements.
Above sheet"per ton consumption (KWH/T)" is a common KGPS parallel intermediate frequency power supply consumption, new technology KGCL series intermediate frequency power supply can saving 15% or more.
※ Complete set configuration: Power supply cabinet, capacitor box, Overturn control box, Furnace body (Steel shell or aluminum shell), hydraulic station (Or Reduction box with stent), water cooled cables etc.
※ The above data is for standard models. We also provide customized non-standard products with different powers or melting speeds.
I. Ordinary KGPS IF parallel power supply, IGBT series IF power supply and the latest model of KGCL series IF power comparative selection
1. Ordinary KGPS Silicon Parallel Inverter IF Power Supply
The advantage: The past few decades has been the most widely used, low price, easy maintenance, Reasonable price of accessories.
The disadvantage: High energy consumption, per ton of molten iron power consumption is about 600 KWH/T. Adjust the DC voltage mode control power, the power factor is low(≤0.90), harmonic interference substation reactive power compensation capacitor running with varying degrees of impact.
2. IGBT Series Inverter IF Power Supply
The advantage: A full-wave rectifier paired with an LC (Inductor Capacitor) filter ensures a power factor above 0.96 and almost no harmonic interference. The series inverter works at high voltage and low current, thus enabling low copper loss and greatly increased efficiency. The energy consumption per tonne of molten steel is below 550kWh.
The disadvantage: IGBT power supply requires a demanding work environment and high maintenance cost.
Full-wave rectification capacitor inductor LC filter power factor above 0.96 almost no harmonic interference
3. KGCL SCR series inverter IF power supply
In the whole work procedure rectifier always in full open state (equivalent to diode rectifier). The power factor of the device is always at the highest state (≧0.96). It does not produce high harmonics. The KGCL saves about 20%, per ton of molten iron power consumption at about 500 KWH/T.
II. Aluminum Shell furnace and Steel Shell furnace Selection
Aluminum Shell furnace: Inexpensive, easy maintenance, convenient observation. The disadvantage is low efficiency, electromagnetic radiation unshielded.
Steel Shell furnace: Made of high quality steel welding, leakage-proof furnace alarm device, inductor around the yoke closure, covering more than 65%, high efficiency, saves nearly 5% energy consumption.
1. Closed Cooling Tower (Recommended)
※ Light weight and small footprint available for free relocation. Available for direct use requiring no pool, pump and piping, etc. to save huge and complex water cooling facilities.
※ Enclosed soft water circulating cooling to prevent piping blockages caused by sundries, protects electric components against scale so as to decrease fault rate of IF, HF and other heating equipment.
※ Automatic digital display of temperature, energy efficient and environmental protection ,easy installation, operation and maintenance.
2. Water Tank Water Pump Open Cooling Tower
The water is pressurized throughout the system and allows for a steady flow with high efficiency heat dissipation.
3. Water Tank Water Pump
The water in the pool is pressurized throughout the equipment and water is recycled back to the reservoir.