CNC Pile Cage Welding Machine
SKZ CNC pile cage welding machine (Mode: KZ1500/KZ2000/KZ2500)
Product IntroductionIn bridge construction, the processing of steel cages plays an important role. Our CNC pile cage welding machine combines steel straightening, bending, and roll welding, achieving basic mechanization and automatic of the cage processing. Our pile cage welding equipment not only reduces the working time and errors in each component, but the quality and efficiency are significantly improved. The CNC cage making machine is known for its capacity in manufacturing cages with excellent economic and social benefits for construction companies and becoming a new development trend in the steel processing industry.
Main FeaturesCompared to traditional steel welding instruments, our CNC welding machine has a number of attractive features.
1. In comparison to traditional manual molding processes, our CNC cage welding machine features a high automation and fast molding speed. It welds 3-4 times as many cages as manual operations did in the past.

2. Stable and reliable quality: A mechanized process ensures the high precision and uniform space between each bar pitch. A mechanical rotation guarantees the close wrapping of reinforced rebars and main bars, and the stirrup will be welded after the forming process. A uniform diameter ensures the concentricity of the reinforcement cage. Our CNC cage welding machine is made in strict compliance with standards and requirements of the industry.
3. At the same production volume as a traditional machine, our machine saves up to 3/4 manpower, significantly reducing processing costs.
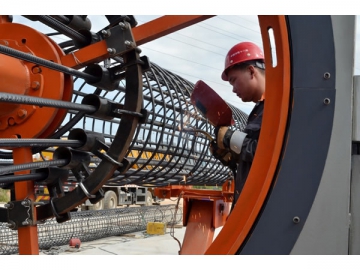
4. The mechanical operation significantly cuts labor of our employees, and allows them to play more of an assistance part, improving the construction process.
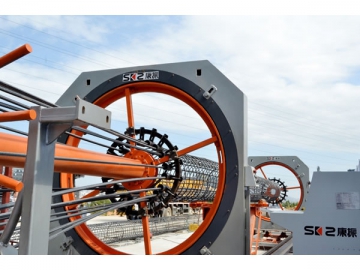
5. Compared to manual operation, the stirrup on the CNC cage making machine requires no joints or connectors and saves up to 1% of raw materials. A normalized structure of main bars also makes the welding of several steel cages simple and easy, saving hoisting time.
Technical Parameters
Model | KZ1500 | KZ2000 | KZ2500 |
Cage diameter (mm) | 500-1500 | 500- 20 00 | 500-2500 |
Cage length (mm) | 2-12 | 2-12 | 2-12 |
Maximum weight of cages (kg) | ≤4500 | ≤ 6000 | ≤8000 |
Diameter of main bar (mm) | 16-32 | 16-32 | 16-32 |
Stirrup diameter (mm) | 6-12 | 6-12 | 6-12 |
Stirrup spacing (mm) | 50-500 | 50-500 | 50-500 |
Total installed capacity (kw) | 18 | 21 | 25 |
Walking speed (m/min) | 1.1 | 1.1 | 1.1 |
Rotating speed (r/min) | 2-3 | 2-3 | 2-3 |
Feeding → insert ing reinforce (main bar) → fixing →overlapping stirrup→ start welding → normal welding→ stop welding → cutting stirrup → Separating fixed disk → loose bar→ separating movable disk→ unloading cage→ lowering electric support→ home movable disk
Technical Solutions 1. Personnel allocation
Under normal circumstances, it requires 5-6 employees to operate. Specific allocations are as follows:
Preparation and feeding of materials: 2 people
Roll welding: 1-2 people
Strengthening hoop: 2 people
The actual personnel allocation will be adjusted according to the size and mode of the steel cage.
1500mm pile cage: Two classes, 300-400 m/unit per day (about 20 tons)
When welding a 12m long steel cage, it takes about 15-20 minutes to feed the materials, and 18-25 to weld, totaling roughly 30 to 45 minutes. Generally, a 12m long steel cage with a diameter of 1.5m weighs about 800kg.
The forming efficiency of the steel cage is related to the number of main bars, the diameter, the pitch of the bars, and the technical degree of employees.
We design different steel cage welding devices based on different project (differences such as changing the main bars or diameter). By changing the template or the pipes, the cage meets different engineering applications.