Die Design
In the past, designing a functional auto die was expensive and time consuming, due to the repeated trial and error processes they underwent. Today, computers aid in the design and modeling process to create the die's design and simulate the stamping process. By doing so, labor and tooling costs in the design process are significantly reduced.
With 18 years of experience, Huanghe has become an expert in stamping die design, and continues to serve the automotive body panel industry. We produce excellent stamping dies for large outer car panels, including cowl panels, body side panels, car fenders, hoods and more car parts. We have supplied products to Changan Suzuki, Geely, Honda, Changan Ford, Jiangsu Jiulong, Fonton Motor, Hawtai Motor and JAC Motors. We have also exported out automotive stamping dies to Italy and Indonesia.
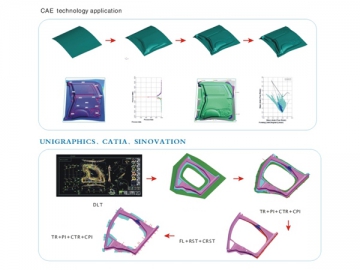
We own and operate an advanced design software and platform, which we use to build a complete line of stamping dies, using UG, CATIA, Autoform, PamStamp, WorkNC and SMIRWARE.
With the use of 3D design and computer based simulations of complicated stamping processes using CAE technology, we can control the quality of each product, with the aid of the SMIRWARE platform, and ensure a satisfactory result for customer's functional needs. With the use of SAP and MES systems, we can also optimize our management and increase the bottom line.
Huanghe employs over 80 professionals from different parts of the stamping dies industry, many of whom are in senior positions and hold a master's degree or higher. We also build a talent pool, where we can educate potential engineers and technicians. We have developed a full, in-house capability for designing and manufacturing draw dies, cam trim dies, piercing dies, and forming dies for body side panels, cowl panels, car roofs, car door panels, car hoods, trunk hoods and floor pans.
Stamping Die Work Flow
1. Technical specs → 2. Stamping → 3.CAE analysis → 4.Structural design → 5. Foam → 6.Castings → 7.CAM → 8. Manufacture→ 9. Assembly → 10. Tryout → 11.Inspection
PDM System
The PDM system not only defines, organizes and manages data in regards to the conceptual design, engineering analysis, detailed design, process flow design, manufacturer, sales, maintenance and servicing of products throughout the lifecycle, but it also serves as the link that joins CAD, CAE, CAM, CAPP, MES, ERP, workshop management, and control systems into one unit. Effective implementation and management of the PD system gives die designers easy access to product specifications without having to sort through piles of documents for the right data. With the PDM system, designers can carry out the following:
1. Improve design efficiency
2. Ensure detailed data is stored in order
3. Allow easy re-use
4. Reduce unnecessary repetitive work
5. Limit the amount of modifications to a particular project
6. Maintain full traceability of all specifications we have delivered in order to facilitate reviews
7. Control the design process
8. Collaborative working environment that supports a concurrent design
9. Facilitate the systematic integration of new product development processes
10. Provide related data to customers in a fast, efficient manner
CAE Technology
Advanced CAE technology can carry out multiple tasks, including the following:
1. Analyze and recoup the amount of kickback in the material from bending
2. Precise modeling
3. Analyze the full process
4. Carryout Pamstamp analysis and mold profile drawings
CAD Technology
Using CAD software, Huanghe's designers can design a variety of tools and dies, including automotive stamping dies, stamping dies for aluminum sheets, flanging dies for outer car panels, multi-station dies, large-scale progressive dies, and blanking dies for laser welded plates.
Smirtware Technology
Using Smirtware technology, multiple operations are easy to carry out, including design inspection, manufacturing, assembly, and die contour processing.
WORKNC Technology
WORKNC is a 3D NC programming software that controls the machine, enabling it to perform processing along the contour line, or according to the 3D drawing.